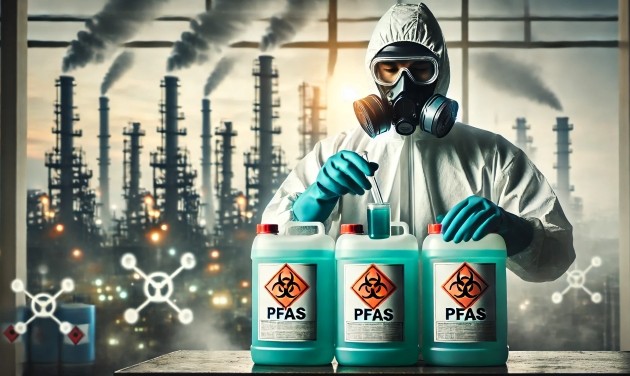
Les matériaux composites, constitués de fibres imprégnées de résines, sont de plus en plus utilisés dans de nombreux secteurs d'activités, notamment dans la construction aéronautique, nautique, automobile, ferroviaire ... La polymérisation à haute température et le dégagement de vapeurs nocives, la découpe des matériaux composites, la superposition de couches (stratification) dans un moule permettant d'obtenir la forme voulue, l’usinage de ces matériaux composites, sont des opérations présentant des risques professionnels chimiques, thermiques, mécaniques importants ...
Les matériaux composites, constitués de fibres imprégnées de résines, sont utilisés de plus en plus dans de nombreux secteurs d'activités, notamment dans la construction aéronautique, nautique, automobile, ferroviaire ...
La polymérisation à haute température et le dégagement de vapeurs nocives, la découpe des matériaux composites, la superposition de couches (stratification) dans un moule permettant d'obtenir la forme voulue, l’usinage de ces matériaux composites, sont des opérations présentant des risques professionnels importants :
- exposition chimique aux composants de résines et aux solvants, aux poussières de fibres (carbone, verre ...), aérosols et vapeurs de composés organiques toxiques (styrène, acétone ...),
- exposition aux risques physiques de la coupe, du fraisage, du polissage et de l’usinage mécanique des pièces moulées,
- exposition aux risques thermiques pendant la phase d’autoclavage, de traitements dans les fours, étuves.
Ces risques chimiques, thermiques, mécaniques, des ateliers de matériaux composites peuvent être maîtrisés par l’utilisation de machines et d’équipements et la présence d’une installation électrique et de protection incendie conformes aux normes, la captation de gaz et de poussières au plus près de leur point d’émission, une ventilation efficace, et par le respect des exigences essentielles de sécurité (lutte contre le bruit, hygiène des locaux...) et de protection individuelle, avec une attention soutenue pendant les périodes de mise en place des outillages et de démarrage de production, ou lors des opérations de maintenance et de réparation.
Les principaux risques des matériaux composites
- Généralités sur les matériaux composites et leur fabrication
Les matériaux composites sont constitués par une matrice organique, résine thermoplastique ou thermodurcissable (polyester ...) et une structure de renfort constituée de fibres entrelacées, qui peuvent être de verre, de carbone, d’aramide ou de textiles naturels.
Un matériau composite résulte ainsi d’un assemblage intime de deux corps à structure différente dont les qualités individuelles se combinent en donnant un matériau hétérogène et anisotrope avec des performances globales améliorées.
La matrice organique lie les fibres de renforts qui constituent l’armature assurant la tenue mécanique, et répartit les efforts.
De charges et additifs peuvent être inclus pour améliorer l’adhérence et modifier les propriétés du matériau (aspect, couleur, anti-UV, ignifugation, isolation thermique ou acoustique).
Les résines époxy sont très utilisées mais on recourt aussi aux résines polyimides (grande résistance à la chaleur), les résines phénoliques, les polyesters et les silicones ...
Les matériaux composites sont d’excellents substituts aux composants métalliques dans de très nombreuses applications, avec une résistance mécanique et thermique égale ou supérieure, et une plus grande légèreté.
Les utilisations des matériaux composites se développent considérablement : depuis les pièces de grandes dimensions de l’aéronautique (voilure, empennage, hélices ...), du ferroviaire (panneaux et aménagement de voitures), de la construction nautique et de la réparation navale (coques, bateaux de plaisance, matériels de sport nautique), de l'industrie éolienne (pales), jusqu’aux pièces de petites dimensions mais de grande série pour véhicules (pare-chocs ...), mobiliers urbains, cuves, articles de sport etc.
La réduction du poids permis par l’utilisation de matériaux composites est un facteur fondamental pour l’abaissement des coûts d’usage des avions et des véhicules terrestres (minimisation de la consommation de carburant) et des couts de fabrication (remplacement de métaux couteux comme l’aluminium et le titane).
On distingue les techniques de transformation des composites qui utilisent des moules ouverts avec des méthodes de moulage par contact ou projection et les techniques de transformation en moule fermé, par exemple le RTM (Resin Transfert Molding), qui ne peuvent pas être utilisées pour les pièces de grande taille destinées, en particulier, à l’aéronautique et à la construction nautique.
Le stratification (ou drapage) est une opération de superposition de couches qui fait appel soit à des techniques par voie humide avec un mélange de résine visqueuse non cuite et de fibres de renfort introduites manuellement dans la résine, soit à l’utilisation de tissus pré-imprégnés se composant de feuilles de composites semi-rigides, partiellement cuites et prêtes à l’emploi.
Les procédés de stratification à moule ouvert incorporant des renforts de fibre de verre amalgamés à une résine liante se font principalement :
- Soit par moulage au contact qui consiste à déposer sur la forme, à la brosse, au rouleau ou au pistolet, une couche d’enduit gélifié (gel coat) et des catalyseurs de polymérisation puis alternativement des couches de renforts (mats ou tissus) imprégnés au rouleau d’une résine polymérisant dans des conditions proches de l’environnement ambiant de l’atelier.
- Soit par projection simultanée : la résine mélangée à un agent de durcissement et à un accélérateur et les fibres de renfort coupées sont projetées ensemble au moyen d’un pistolet sur une forme ;
- Soit par compression qui consiste à comprimer la matière dans un moule ouvert et chauffé.
L'injection de thermoplastiques renforcés, le moulage en autoclave, l’estampage thermoplastique, le moulage en compression, le formage sous vide ou en autoclave, sont des procédés industriels mécanisés et éventuellement de mise en œuvre en continu (machine à draper, machine de pultrusion ...) dont certains exigent des hautes températures et des pressions très élevées.
Puis les opérations d’usinage et de finition des pièces en matériaux composites permettent une mise à longueur, l’ébarbage, la création de trous de fixation ... à l'aide d'outillages portatifs ou de machines-outils : coupe, perçage, alésage, détourage, surfaçage avec des machines à découper, perceuse, ébarbeuse, ponceuse, polisseuse, meuleuse ... - Les risques chimiques des matériaux composites
Lors de la transformation des matières plastiques et de la polymérisation, l’élévation de la température peut entraîner la libération de produits volatils potentiellement dangereux.
Les usines utilisant des matériaux composites se caractérisent par des environnements chimiques très complexes. Les ouvriers des matériaux composites (stratifieurs ou drapeurs) peuvent être exposés à des produits chimiques dangereux en phase liquide (vapeurs d’acétone ...) ou gazeuse (émanations de styrène ...) ainsi qu’à diverses poussières de fibre de verre ou de carbone, ce qui constitue des risques respiratoires. Un contact direct avec les résines, les catalyseurs, ... peut causer des lésions à la peau. Les technologies de transformation des composites exposent ainsi les stratifieurs aux émissions toxiques des composés organiques volatils (COV), tel le styrène contenu dans les polyesters insaturés, en particulier pour certaines étapes de la fabrication, selon la nature des procédés utilisés : l’utilisation de procédés de transformation en moule ouvert (moulage au contact, projection) peut conduire à une exposition plus importante des opérateurs, de même l’exposition chimique aux composants de résines et aux solvants lors des opérations de stratification humide est bien supérieure à celle de la stratification avec des feuilles pré- imprégnées.
La pose et l’enlèvement répétés de bandes de matériaux composites peuvent libérer des mélanges solvant-résine sous forme d’aérosols.
Les composants les plus dangereux sont les amines aromatiques utilisées comme réactifs dans les résines polyimides et les durcisseurs des systèmes à base de résine époxyde. Un certain nombre de ces composés sont des cancérogènes confirmés ou soupçonnés. Ils ont également d’autres effets toxiques, dont une sensibilisation cutanée et respiratoire.
L’usinage mécanique des pièces moulées peut produire des poussières irritantes respiratoires, associées aux matériaux de renfort (fibres de verre, carbone, kevlar).
Il faut aussi tenir compte des gaz toxiques de décomposition des lubrifiants et des poussières abrasives émis par les machines et les outils lors de l’usinage.
- Aspects toxicologiques des résines et de leurs diluants et durcisseurs
L’exposition aux vapeurs de solvants et aux poussières des résines, représente un souci majeur. Une exposition non contrôlée à ces agents peut entraîner des troubles du système nerveux central, des atteintes hépatique et rénale ou des réactions de sensibilisation.
Les résines avant polymérisation ou en poussières libérées par des opérations d’usinage ou de ponçage peuvent être responsables de réactions d'irritation, de sensibilisation et d'allergie de la peau avec eczéma de contact touchant les doigts, les mains, les poignets et les avant-bras mais aussi le visage avec œdème des paupières par projection de particules.
La dermatite de contact allergique aux résines apparaît suite à la sensibilisation progressive à ces produits de façon spécifique du fait de la multiplicité des contacts cutanés non protégés. L'eczéma de contact siège sur les faces dorsales et latérales des doigts et des mains, face interne des poignets.
Les atteintes cutanées sont érythémateuses avec lésions prurigineuses, vésiculeuses suivies d'une phase de suintement, de formation de croûtes et de desquamation, et l’eczéma peut se surinfecter.
Les constituants volatils des durcisseurs aminés (triéthylènetétatramine ...) sont susceptibles de provoquer des actions d’irritation ou de sensibilisation des voies respiratoires. Les amines aromatiques possèdent des cycles de type benzénique ayant un caractère cancérogène (cancers de la vessie).
Les polyisocyanates sont allergisants en cas de contact cutané ou d’inhalation, et risquent de provoquer des de l’asthme et de l’eczéma, des pneumopathies d'hypersensibilité, des blépharo-conjonctivites.
Les solvants et diluants organiques des résines (styrène, acétone, méthacrylate de méthyle ...) affectent des organes cibles divers : irritations de la peau, des yeux et de la gorge, lésions des organes et presque tous les solvants organiques provoquent des troubles digestifs du système nerveux, des maux de tête, des vertiges. Par leur action liposoluble, tous les solvants peuvent provoquer une dessiccation cutanée avec risque de dermatites pour des contacts avec la peau répétés et prolongés. La toxicité des solvants organiques sur le système nerveux central peut prendre la forme d’une narcose brutale et intense pour une forte exposition.
Les maladies professionnelles d’origine chimique des stratifieurs font l’objet de plusieurs codifications dans le Régime Général de la Sécurité Sociale :
Tableau n°51 RG : Maladies professionnelles provoquées par les résines époxydiques et leurs constituants
Tableau n°62 RG : Affections professionnelles provoquées par les isocyanates organiques
Tableau n°65 RG : Lésions eczématiformes de mécanisme allergique
Tableau n°82 RG : Affections provoquées par le méthacrylate de méthyle
Tableau n°84 RG : Affections engendrées par les solvants organiques liquides à usage professionnel
- Aspects toxicologiques des poussières des fibres de renfort
Pour les fibres de renfort, le risque pour les produits eux-mêmes est faible, mais ce sont les poussières fibreuses éventuellement générées lors de leur utilisation qui sont nocives.
Le problème majeur lié à l’exposition professionnelle à des fibres est ainsi l’inhalation de ces fibres ou de leurs poussières émises lors des opérations d’usinage : en effet, les fibres réussissent à traverser la cavité nasale et à s'attaquer à la trachée, atteindre les alvéoles pulmonaires et les cellules des bronches, et s’y accumuler. En séjournant longtemps dans le tissu pulmonaire, elles engendrent une inflammation des muqueuses pulmonaires, la formation d'un tissu pulmonaire fibreux (fibrose entrainant une insuffisance respiratoire). Dans le cas des fibres de renfort des matériaux composites, moins fines par rapport à celles de l’amiante par exemple, elles sont capables de produire une réaction fibrogéne seulement légère et la susceptibilité individuelle est différenciée à la fois par des composantes génétiques et par d’autres expositions pathogènes personnelles, dont la plus sensible est le tabagisme.
Par ailleurs, l’inhalation constante dans les poumons de fibres peut causer des rhinites allergiques ou des inflammations de la muqueuse nasale, des pneumopathies chroniques et de l’asthme.
Le contact cutané avec les fibres peut provoquer aussi des dermites d’irritation qui se traduisent par des lésions plus ou moins importantes telles des rougeurs, des démangeaisons (prurit) et de l’urticaire ou de l’eczéma.
La valeur limite d’exposition à respecter est fixée en moyenne (à ce jour) :
- pour les fibres de verre, à 1 fibre par cm3, sur 8 heures
- pour les fibres de carbone, peu fines et donc peu inhalables, les risques de fibrogénèse ou de cancérogénèse paraissent faibles et une valeur limite maximale à 3 fibres par cm3 est préconisée.
Toutefois, ces fibres pourraient se scinder en microfibrilles plus fines pouvant atteindre les alvéoles du poumon en profondeur lors de certaines opérations comme le ponçage. - Les risques thermiques des stratifieurs
Toutes les machines de transformation, les autoclaves, les étuves et fours de séchage utilisent un apport de calories par chauffage ou par le biais d’accélérateurs de chaleur, provoquant des températures de transformation qui s’échelonnent de 150° à 300° environ pour permettre la polymérisation.
Du fait de ces procédés, les locaux des ateliers des matériaux composites sont donc particulièrement exposés aux températures élevées et aux risques de brûlures thermiques.
La proximité d’une source de chaleur peut entrainer des céphalées, hypersudation, tachycardie, hypotension et, conjuguée à des températures de l’air élevée, provoquer des malaises dus à la déshydratation et des troubles circulatoires. Au-delà de 25 oC, l'inconfort se fait ressentir avec, de plus, toutes les conséquences psychologiques que cela peut avoir sur la précision des gestes, la vigilance et donc la sécurité (diminution des capacités de réaction, irritabilité, agressivité).
Les brulures peuvent notamment survenir lors du contact avec les canalisations transportant les fluides caloporteurs pendant les périodes de montage, réglage et maintenance.
Les brulures peuvent aussi être provoquées par des surpressions occasionnant des projections chaudes de matière plastique par les orifices de dégazage, d’alimentation et des buses. - Les risques physiques des stratifieurs
- Les vibrations
Les vibrations de machines-outils portatives (ponceuses, meuleuses ...) sont à l’origine d’effets pathologiques sur le membre supérieur (main, coude, épaule), tandis que celles de certaines machines fixes mal calées affectent surtout la colonne vertébrale par transmission des vibrations au corps entier.
Les expositions des stratifieurs aux vibrations entrainent des troubles ostéoarticulaires (tendinites, lombalgies...), neuropathiques (mal carpien...) et vasculaires.
- Les manutentions
Les charges lourdes portées manuellement, ou le nombre excessif de manipulations et mouvements avec torsion du dos, rotation pour le déplacement, flexion pour le soulèvement (lors des changements de moules par exemple), ou la station debout prolongée ... sont à l’origine d'accidents de travail concernent la colonne vertébrale (dorsalgies, lombosciatiques) et le vieillissement progressif des structures ostéoarticulaires.
- Les incendies et explosions
Les ateliers de plasturgie sont confrontés à un risque potentiel d’inflammation des solvants et d’explosion des poussières de matières plastiques due aux décharges électrostatiques, avec des sources de chaleur nombreuses provoquant de redoutables incendies à la mesure de la quantité de matières plastiques inflammables présentes dans l’atelier, dont la combustion dégage des gaz et fumées très toxiques.
Les risques d’incendie-explosion sont présents dans le cas de concentrations de styrène dans l’air atteignant les limites d’explosivité. Le stockage des résines dans des sacs endommagés dans des espaces clos et mal ventilés peut provoquer l’accumulation de vapeurs inflammables.
- Autres risques des stratifieurs
D’autres risques ne sont pas spécifiques au métier de stratifieurs, mais communs à toute activité industrielle : chutes de plain pied sur sol glissant, inégal ou encombré, coupures aux mains ou écrasements, ou lors des déplacements des éléments mobiles des machines, entraînement par des rotors ou cylindres en rotation, projections de corps étranger dans les yeux, électrisation/électrocution par utilisation d’outillage défectueux ...
Les mesures préventives des risques des matériaux composites
Le process des fabrications des pièces en matériaux composites en grandes séries est mécanisé et automatisé (machines robotisées, centres d’usinage, ...), ce qui réduit considérablement les risques thermiques, physiques (manutention, coupures...), chimiques et acoustiques. Toutefois, des incidents dans l’automatisation des opérations, des fuites, nécessitent des interventions de maintenance qui restent dangereuses. Par ailleurs, dans les petites séries, les pièces sont élaborées avec des procédés beaucoup plus manuels et les pratiques sécuritaires doivent être particulièrement bien mises en œuvre et maîtrisées.
Les ateliers des fabrications en composites doivent faire l’objet d’une analyse poussée des risques pour permettre la rédaction du Document Unique de Sécurité (Décret du 5 novembre 2001) en appréciant à la fois l’environnement matériel et technique (outils, machines, produits utilisés) et l’efficacité des moyens de protection existants et de leur utilisation selon les postes de travail.
Les analyses de risques sont confiées à des spécialistes de la sécurité au travail (hygiéniste, ingénieur sécurité). Les rapports d’intervention et de maintenance seront aussi intégrés à la documentation de sécurité au travail de l’entreprise et communiquées au médecin du travail et au CHSCT.
La prévention la plus efficace est la prévention primaire avec la mise en place de technologies qui permettent des actions sur les produits (suppression ou emploi de produits de substitution de moindre impact potentiel sur l'homme) et/ou des actions sur les procédés (emploi de matériels ou de machines supprimant ou limitant au maximum les impacts, par de très faibles rejets atmosphériques, par de bas niveaux sonores...).
Les moyens de prévention à mettre en œuvre pour pallier les risques professionnels dans les industries des matériaux composites résident ensuite dans la prévention collective (ventilation efficace de l’atelier et aspiration à la source des poussières et fumées, stockage des produits chimiques et installation électrique et de protection incendie conformes aux normes, respect des règles générales d’hygiène...) qui diminue fortement les expositions et la fréquence ces accidents, puis dans la prévention individuelle (équipements de protection) qui en diminue nettement la gravité, enfin dans la l’information et la formation à la sécurité des travailleurs.
Les salariés doivent être aussi informés à propos des produits dangereux utilisés et formés aux pratiques professionnelles sécuritaires.
Par ailleurs, une surveillance médicale renforcée est obligatoire pour les salariés exposés aux risques chimiques des industries des matériaux composites.
- La suppression / substitution des produits les plus toxiques
Le remplacement des techniques de transformation en moule ouvert par des techniques en moule fermé doit s’imposer quand c’est techniquement et économiquement possible : c’est ainsi que les techniques de transformation en moule fermé, par exemple les procédés de moulage sous vide ou des procédés de type RTM, ne peuvent que difficilement se substituer aux méthodes de moulage par contact ou projection pour les pièces de grande dimension dans la construction aéronautique ou nautique.
- L’utilisation de machines et équipements adaptés
- La réduction des risques au cours des opérations de stratification par voie humide doit inclure une ventilation avec aspiration localisée.
Les déchets de coupe, de meulage et de polissage doivent être aussi totalement éliminés avec une aspiration à la source sous basse ou haute dépression et collecte des poussières et des particules, puis filtrage de l’air avant d’être recyclé dans les locaux ou rejeté à l’extérieur dans l’atmosphère. - Systèmes d'encoffrement et de captage au plus près des émissions, de façon à évacuer les aérosols et les vapeurs :
Il convient de doter les installations de captages localisés et avoir des dispositifs de captage au dessus de l’ensemble des équipements (hottes aspirantes, plafonds filtrants ...), en particulier au niveau des moules lors de l’injection ou de la projection de la matière plastique, afin de maintenir un niveau d’exposition inférieur aux limites réglementaires. - Les outils de la stratification manuelle doivent être adaptables à la taille de la main.Des outillages réglables doivent être également employés pour positionner la pièce de manière confortable pour le travail.
- Dispositifs de sécurité des machines :
Toute machine doit porter les avertissements, signalisations et dispositifs d’alerte indispensables pour assurer la sécurité des travailleurs afin de supprimer ou réduire au minimum les risques de coupure, d’entraînement, d’écrasement, de cisaillement causés par les éléments exerçant une action directe sur la matière. Cette identification doit être réalisées par des pictogrammes et couleurs normalisées. Les éléments de travail doivent être disposés, protégés, commandés ou équipés de façon telle que les opérateurs ne puissent atteindre la zone dangereuse.
Les panneaux de signalisation seront choisis et disposés de façon à être perçus et compris facilement sans ambiguïté.
Chaque machine doit être munie d’un ou plusieurs dispositifs d’arrêt d’urgence clairement identifiables, accessibles et en nombre suffisant, permettant d’éviter les situations dangereuses en train de se produire :
• Ecrans de protection et de sécurité des opérateurs : protecteurs fixés à l’aide de moyens imposant un outil pour leur démontage ou par des protecteurs mobiles associés à un dispositif de verrouillage.
• Interrupteurs de sécurité.
• Barrières immatérielles de sécurité : des dispositifs électrosensibles de détection de présence et /ou de mouvement verrouillent les mouvements des parties mobiles pendant la présence d’un opérateur.
• Embouts spéciaux antiarrachements
• Capteurs pour mesurer les températures et réguler les dispositifs de chauffage et éviter les surchauffes productrices d’émanations de décomposition thermique dangereuses
• Capteurs pour mesurer les pressions et réguler les dispositifs mécaniques et thermiques et éviter les surpressions internes.
• Ces capteurs sont intégrés dans des systèmes de commande et de contrôle gérés par des automates programmables.
• L’éloignement du personnel des zones dangereuses se fait au moyen d’obstacles fixes tels que panneaux fixes, pleins ou grillagés.
• Sécurisation de l’installation au moyen de clapets anti retour, d’écrans anti-projections, etc. - Le respect des recommandations des constructeurs et un entretien régulier des machines sont des éléments essentiels pour limiter les risques accidentels et pour prévenir des émanations. Ainsi l’utilisation et l'entretien des machines doivent être effectués par un personnel qualifié, spécifiquement formé (respect scrupuleux des capacités nominale des machines...) : de nombreux cas de fuites accidentelles peuvent survenir au niveau de différents équipements, ce qui entraîne la nécessité d’une maintenance rigoureuse des machines avec contrôle de l'étanchéité.
Des machines utilisées de manière non conforme ou mal entretenues et non vérifiées périodiquement créent un risque chimique supplémentaire. En particulier, les canalisations flexibles doivent être vérifiées périodiquement et remplacées en cas d’usure ou de choc, et en fonction de la durée maximale d’utilisation.
- Une ventilation des lieux de travail adéquate
Les multiples risques chimiques que présentent les matériaux composites ont conduit à de nombreuses réglementations, aboutissant à un ensemble complexe de mesures pour répondre aux normes (valeurs limites d’exposition professionnelle).
La ventilation et l’aération des lieux de travail jouent un rôle essentiel pour limiter la concentration de l'ensemble des toxiques dans l'air ambiant et les évacuer des lieux de travail, de façon à respecter ces valeurs limites et éviter ainsi les conséquences sur la santé des travailleurs. Une ventilation et un appoint d’air appropriés sont aussi indispensables pour empêcher l’accumulation de mélanges inflammables dans l’air. En particulier, une ventilation adéquate des zones de moulage est importante en raison des quantités importantes de vapeur dégagée par les procédés de moulage.
Les installations utilisées doivent faire l’objet d’une analyse de risques et de relevés métrologiques périodiques : surveillance régulière de l'atmosphère, pour vérifier l'efficacité des mesures d'aspiration par dosages atmosphériques.
La ventilation mécanique générale doit assurer un renouvellement d'air en permanence afin de limiter les risques pour la santé, en évitant l’accumulation de vapeurs nocives et explosives, par extraction et soufflage : l'air est transporté dans le local par un ventilateur de soufflage et extrait du local par un ventilateur d'évacuation. L’extraction de l'air se fait grâce à un système de collecte par ces ventilateurs, des gaines de diffusion, et un réseau de conduits qui captent et concentrent les poussières et vapeurs jusqu'aux filtres et aux épurateurs qui permettent de nettoyer l'air, puis de l’évacuer à l'extérieur par rejet dans l'atmosphère. La ventilation générale des ateliers doit être déterminée en fonction des aspirations locales pour ne pas perturber l’efficacité des captages à la source.
Les composants aérauliques comme les ventilateurs, les conduits entre autres doivent être accessibles et faciles d’entretien et de nettoyage. En particulier, les réseaux s’encrassent rapidement avec de filtres hors d’usage, une évacuation des condensats obstruée...
- Une installation électrique conforme
L’incendie et/ou l’explosion peuvent provenir des équipements électriques, et en particulier, l’équipotentialité et la bonne mise à la terre de toutes les installations métalliques doivent être contrôlées, les prises défectueuses remplacées, il faut éviter toute accumulation d’électricité statique ....
Les étincelles, arcs et échauffements provoqués par les moteurs et appareillages électriques en fonctionnement peuvent aussi déclencher la catastrophe.
Il convient d’utiliser de l’appareillage électrique conçu pour atmosphères dangereuses afin de prévenir que le matériel, y compris l’éclairage, soit à l’origine d’un incendie ou d’une explosion.
Une métallisation au moyen d’un matériel conducteur et une mise à la terre appropriées de l'équipement de traitement et de manutention sont utiles pour dissiper et diriger à la terre en toute sécurité les charges électriques accumulées. La protection contre les contacts avec les masses mises accidentellement sous tension est obtenue par un dispositif de coupure automatique en cas de défaut d’isolement.
Il est fortement recommandé de placer des explosimètres dans les zones de réception / manutention / stockage / expédition.
Dans le domaine des atmosphères explosives (Atex), des normes européennes fixent le cadre de travail des industriels et des installateurs. Depuis juin 2003, tout nouveau site de type Atex doit être équipé avec du matériel certifié, avec des enveloppes antidéflagrantes. Les autres installations doivent, depuis juin 2006, avoir été mises à niveau.
- Un stockage des produits rigoureux
Le stockage des composants présente des risques tels que l’incendie, l’explosion, le risque de chute ou de renversement ou de détérioration d'emballage ... Toutes ces caractéristiques rendent nécessaire, outre les précautions lors de leur emploi, l’aménagement de locaux de stockage, avec des rayonnages métalliques, des planchers et des palettes normalisées. La réduction des risques existants passe par une réflexion sur la structure du local, sur les modalités de rangement et sur les incompatibilités entre les produits. Des procédures de stockage non adaptées peuvent entraîner une fragilisation des emballages à l'origine de fuites ou de ruptures accidentelles, de pollution, de réactions dangereuses ou d'accidents ou induire une modification ou une dégradation des produits qui le rendent plus dangereux car ils peuvent libérer des vapeurs inflammables ou nocives.
L’empilement doit être stable et sa hauteur ne doit pas affecter l’intégrité des emballages.
Le stockage des bidons de solvants, sacs, boites d’adjuvants ..., doit se faire dans un local ventilé par un système de ventilation mécanique, à l'abri de la chaleur et de l'humidité, et tous les conteneurs de produits chimiques doivent toujours être bien refermés.
L'installation électrique du local de stockage est à réaliser avec du matériel utilisable en atmosphère explosible.
Une bonne tenue des sols des locaux de stockage est essentielle pour éviter l’accumulation des matières déversées.
L’interdiction de fumer dans les locaux doit être absolument respectée et signalée de manière apparente (de même que toutes les autres consignes de sécurité).
Il faut stocker les plus faibles quantités de produits possibles car le risque d'incident ou d'accident croît avec la durée et le volume de stockage.
- La lutte contre le bruit
Par le choix ou l’achat de machines et par l’utilisation de procédés silencieux, les émissions sonores peuvent être maintenues à un bas niveau.
Les machines bruyantes seront, selon les possibilités, munis de capots insonorisants et pour réduire les bruits transmis par les sols et les structures, des blocs anti-vibrations peuvent être placés entre la machine et la surface d’appui.
Les échappements d’air comprimé des circuits pneumatiques sont à équiper d’un silencieux. Les postes de commande et de contrôle peuvent se situer dans un local séparé avec une isolation phonique.
En ce qui concerne les locaux, les réflexions sur les murs entraînent une augmentation du niveau sonore dans le local et des mesures préventives de correction acoustique comme la mise en place d’un plafond absorbant, de cloisons amovibles à proximité des installations, réduisent à la fois le niveau sonore et protègent les postes de travail avoisinants.
- Un bon entretien des locaux
Une bonne tenue des locaux est essentielle pour éviter l’accumulation de déversements et de poussières sous ou autour des machines de moulage. Les déversements peuvent créer un danger de glissement et par conséquent doivent être nettoyés immédiatement. De même, il convient de ramasser et enlever la poussière créée par les opérations de découpage et de ponçage etc.
- Des aides à la manutention
Les nombreuses manutentions manuelles de charges lourdes qui entraînent des risques évidents de troubles musculo-squelettiques au niveau du dos et des articulations, peuvent être réduits par l’utilisation systématique de manutention assistée et de moyens de mise à niveau et de préhension des charges, en particulier des moules : ponts roulants, chariots, moyens de levage appropriés...
- Le port d’équipements de protection individuel adéquat
Les équipements de protection individuelle sont nécessaires pour réduire le risque d’exposition non totalement éliminé par les mesures de protection collectives précédentes : masques respiratoires filtrants, gants, vêtements de protection, chaussures et lunettes de sécurité.
En cas d’urgence ou pour des travaux exceptionnels d’entretien de courte durée (ponçage ...) dans des atmosphères polluées par des vapeurs de solvant organique et de résine, ou lors de travaux en milieu confiné, si le système de ventilation ne suffit pas à empêcher l’accumulation de vapeurs ou de poussières, un appareil de protection respiratoire adéquat doit être fourni : masque à cartouche avec un filtre adapté au produit (par exemple masque FFA2P3D pour une protection contre les vapeurs organiques, masque anti-poussière FFP3 ... ).
Il s’avère indispensable de porter des gants de protection adaptés à la tâche effectuée et au produit manipulé : il n'existe pas de gant de protection universel. Le type de gants conseillé, imperméables, à longues manchettes, pour éviter la pénétration des produits à l’intérieur, doit être adapté aux différents produits manipulés selon leur composition qui figure sur la Fiche de Sécurité (par exemple gants de protection chimique en Viton ®). Le port des gants est obligatoire lorsque l’étiquetage du produit à manipuler comporte les phrases de risque R27 (très toxique par contact avec la peau), R24 (toxique par contact avec la peau), R21 (nocif par contact avec la peau), R34 (provoque des brûlures) et R35 (provoque de graves brûlures).
Il est recommandé de porter des vêtements à manches longues et des combinaisons aux propriétés antistatiques et ininflammables, surtout lors des interventions près des surfaces chaudes (moules chauffés...) et sur les circuits de fluides caloporteurs.
Il convient de se munir de lunettes de protection lors de travail par projection ou de ponçage et découpage de matériaux composites.
- Le respect des règles d’hygiène et de sécurité
Des lavabos, postes de rinçage oculaire et des douches de sécurité doivent se trouver à proximité des postes de travail. Celles-ci permettent les mesures d'hygiène générale : lavage des mains fréquent avec lave-mains à commande non manuelle (au genou, au coude, électronique), douche en fin de poste... En effet, le respect des règles d’hygiène s’étend aux comportements individuels : ne pas avoir les mains sales afin de ne pas ingérer par inadvertance un produit toxique et ne pas manger sur le lieu de travail.
Le contact répété des solvants avec la peau entraînant un dessèchement cutané prédisposant aux dermatoses : aussi, il convient, pour l’hygiène des mains, de se laver les mains et les avant-bras après le travail et avant de manger en utilisant un savon adapté et/ou une fontaine de dégraissage et sans jamais utiliser de solvant organique comme détachant.
Le personnel doit avoir à sa disposition des vestiaires et des sanitaires correctement équipés et en nombre suffisant. Des vestiaires doubles doivent être mis à la disposition des travailleurs : l’entreposage des tenues de travail doit avoir lieu à l’abri de la poussière et des souillures (le rangement des tenues de ville et des tenues de travail doit être séparé).
Les consignes en cas d'accident (n° d'appel d'urgence, conduite à tenir, identification des services de secours) doivent être visiblement affichées.
Une trousse contenant le matériel de premiers secours non périmé doit être mise à la disposition du personnel, toute blessure cutanée doit immédiatement être désinfectée et pansée. Une projection oculaire de résine ou de durcisseur humide est une urgence ophtalmologique.
- Une surveillance médicale renforcée
Pour les stratifieurs exposés aux vapeurs organiques et aux poussières, il faut réaliser des visites médicales régulières dans le cadre d’une surveillance médicale renforcée.
Généralement, il y a un long délai entre l'exposition et le diagnostic d’une maladie professionnelle, ce qui nécessite une traçabilité au travers de la rédaction d’une fiche d'exposition et d’une surveillance médicale régulière, à visée de dépistage, réalisées par le médecin du travail.
A sa sortie de l’entreprise, le travailleur exposé doit recevoir une attestation d’exposition qui lui permettra de continuer à se faire suivre médicalement.
Les modalités générales de la surveillance des travailleurs exposés à des agents chimiques dangereux sont les suivantes :
- Suivi médical et toxicologique régulier, au moins annuel (exemples : tests respiratoires, hématologiques, allergiques ...).
- En cas d'anomalie, tout le personnel concerné doit bénéficier d'un examen médical.
- Fiche d'aptitude avec mention de l'absence de contre-indications médicales à l'exposition au risque après étude du poste de travail.
- Le dossier médical doit stipuler la nature du travail effectué, la durée des périodes d'exposition et les résultats des examens médicaux. Ces informations sont indiquées dans l'attestation d'exposition et le dossier médical doit être conservé après la cessation de l'exposition.
- La formation et l’information du personnel
La formation, par un organisme agréé, sur les dangers des produits utilisés et sur les moyens de se protéger, est indispensable : par exemple, comprendre les étiquettes du contenant des produits, connaître l’attitude à adopter en cas de fuite ou de déversement accidentel, savoir utiliser les E.P.I adéquats, formation aux premiers secours et incendie...
JUIN 2016
Partagez et diffusez ce dossier
Laissez un commentaire
Votre adresse de messagerie ne sera pas publiée.