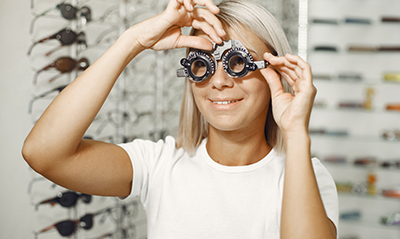
La prévention des risques en maintenance. Les interventions de maintenance préventive (nettoyage, vérification électrique, graissage des roulements, changement de pièces d’usure…) sont régulières et planifiées, alors que les interventions de maintenance corrective (diagnostic de la cause d’une panne de machine, remplacement des pièces défaillantes, réglages et remise en service…) sont inopinées et urgentes...
Le technicien de maintenance effectue à la fois une maintenance préventive de surveillance et d’entretien courant (destinée à réduire la probabilité de défaillance ou de dégradation du fonctionnement) et une maintenance corrective sous forme d’interventions plus lourdes et compliquées de dépannage sur les machines d'un atelier ou les installations techniques d’un bâtiment.
Les interventions de maintenance préventive (nettoyage, vérification électrique, graissage des roulements, changement de pièces d’usure…) sont régulières et planifiées, alors que les interventions de maintenance corrective (diagnostic de la cause d’une panne de machine, remplacement des pièces défaillantes, réglages et remise en service…) sont inopinées et urgentes.
450 000 salariés travaillent en France dans la maintenance, dont 250 000 dans le secteur industriel et 200 000 dans le bâtiment résidentiel ou tertiaire.
Les informations collectées et analysées par l'association AFIM (Association Française des Ingénieurs et responsables de Maintenance) ont établi un état des lieux préoccupant en termes de santé et de sécurité pour les métiers de maintenance :
- une occurrence d'accident grave 3 fois supérieure à la moyenne nationale,
- une occurrence de maladie 6 fois supérieure,
- une occurrence de mortalité 8 fois supérieure.
En effet, le personnel de maintenance est amené à effectuer de nombreuses interventions :
- qui ne sont pas toujours répétitives et par suite, soumises à de nombreux aléas ou situations inhabituelles,
- très diversifiées, souvent conduites sur des équipements en fonctionnement,
- sur des éléments d’équipements ou de machines difficilement accessibles au démontage et au remontage, et/ou lourds à manipuler,
- exposant au contact avec des pièces nues sous tension ou fluides sous pression,
- avec une pression temporelle forte, surtout si la machine en cause est vitale pour la production,
- avec une lourde charge mentale pour des systèmes industriels automatisés qui deviennent plus complexes et donc plus difficiles à maintenir en état,
- souvent sous-traitées, donc avec du personnel connaissant peu ou pas du tout les lieux,
- qui peuvent s’effectuer de jour comme de nuit,
- souvent dans des espaces clos, mal éclairés, exigus voire insalubres, …
C’est pourquoi ces conditions de travail soulèvent généralement des problèmes de sécurité, et par conséquent doivent faire l’objet d’une attention particulière pour en maîtriser les risques
Par ailleurs, plus encore que dans toute autre activité, les accidents liés à la maintenance se caractérisent par leurs causes multiples : cela augmente d’autant les risques dans un secteur où le salarié y est, par nature, davantage exposé que dans la production.
La prévention des risques professionnels ne peut pas être identique pour une maintenance préventive, effectuée régulièrement et préparée, ou pour une maintenance corrective, effectuée inopinément : dans le premier cas, on peut prévoir les dispositifs de protection qui permettront de minimiser les risques d'accidents ou d'exposition, dans le deuxième cas, une analyse des risques spécifiques devra être menée préalablement à chaque intervention afin de procéder à la mise en place des procédures et outils de prévention adéquats.
L’intégration des exigences de maintenance lors de la conception des machines est une étape nécessaire pour que les utilisateurs finaux de la machine ne se retrouvent pas avec des machines trop difficiles ou dangereuses à entretenir.
De même, il est essentiel, dès la conception d’un lieu de travail, bâtiment industriel ou tertiaire, de prévoir le déroulement des opérations de maintenance et d’envisager les interventions ultérieures sur l’ouvrage. L’équipe de conception doit prendre en compte l’ensemble de ces impératifs afin d’intégrer des dispositifs et d’assurer la santé et la sécurité des opérateurs.
Le Plan de Prévention
La nécessité d'une évaluation des risques est à la base de la mise en oeuvre d'une démarche de prévention. Les risques sont démultipliés lorsque plusieurs intervenants sont amenés à travailler simultanément sur la même installation.
Or, la sous-traitance de la maintenance est externalisée de plus en plus dans les entreprises industrielles et ainsi la gestion de la sécurité doit être partagée, concertée entre les entreprises intervenantes et utilisatrices pour limiter les risques de « co-activité ». Le rôle de la coordination " Maintenance - Fabrication " dans la maîtrise des risques liés aux interventions sur les installations est important : la formalisation des relations est plus complexe lorsque les travaux de maintenance sont effectués par une entreprise extérieure, en particulier lorsqu'elle est nouvelle ou qu'elle intervient occasionnellement (difficultés de transmission des informations, indisponibilité par mobilisation de l'encadrement et du personnel de production sur les conséquences de l’incident de fabrication …).
Pour réduire ces risques, un planning très rigoureux qui organise les étapes d’intervention des différentes entreprises sur le site doit être établi en amont, avec certaines règles communes, comme par exemple, les coupures d’eau, d’électricité, mais aussi le balisage et la signalisation, les équipements de protection…Les détails de cette organisation sont décrits dans un Plan de Prévention que la loi impose avant le commencement des travaux si le nombre total d'heures de travail prévu pour réaliser les travaux est au moins de 400 heures sur 12 mois, ou bien si les travaux figurent sur la liste des travaux dangereux fixé par l'arrêté du 19 mars 1993 (Article R. 4512-6 du code du travail : plan de prévention, Article R. 4512-7 du code du travail : plan de prévention écrit).
Les procédures de consignation
De nombreux accidents surviennent suite à une demande de mise en fonctionnement alors qu’une intervention est en cours ; ou bien, les circuits hydrauliques n’ayant pas été purgés, il y a eu libération de l’énergie accumulée et mouvement pendant une intervention…
Pour mettre les intervenants de maintenance en sécurité, la consignation est l’ensemble des moyens de protection mis en place temporairement sur des équipements ou sur des machines, dispositions qui permettent de les mettre et de les maintenir en sécurité.
Il s’agit d’éviter une mise en route intempestive de l’équipement de travail sur lequel on effectue une intervention (même mis à l’arrêt), non séparé de sa source d’énergie ou de la libération d’une énergie résiduelle (tension électrique, pièces mécaniques en mouvement, fluides sous pression…).
La procédure de consignation comporte :
- la séparation de cet équipement de ses sources d’énergie Electrique/pneumatique/hydraulique/mécanique pouvant
- provoquer des mouvements : électricité, air comprimé, huile hydraulique
- provoquer des incendies, des explosions, des brûlures
- provoquer des électrocutions, des intoxications (gaz, vapeur, CO), des irradiations.
- provoquer des projections (poussière, matières incandescentes, gaz) - la condamnation de cette séparation.
Tout organe qui a permis la séparation d'un équipement de travail de ses sources d'énergie doit être immobilisé en position de sécurité par mise en place de verrouillage physique :
- ouverture : pour un circuit électrique, une vanne de purge,
- fermeture : pour un fluide.
Cette condamnation peut être réalisée soit :
- par verrouillage mécanique (Exemple : Cadenas sur sectionneur local)
- par suppression ou enlèvement de l'organe de connexion (vanne, courroie, accouplement,...)
- par placement d'une barrière (joint plein,...).
La condamnation doit toujours être signalée par affichage pour information claire et permanente de la réalisation de la condamnation (étiquettes de consignation…) - la dissipation des énergies accumulées.
Annulation de toutes les énergies résiduelles. - la vérification de la non alimentation en énergie de l’équipement.
Avant intervention, la zone d’intervention devra être délimitée et balisée. Avant toute intervention sur un équipement le chargé de consignation s'assure :
- qu'une analyse de risque a été réalisée,
- que les modes opératoires de consignation et de déconsignation sont définies et à disposition,
- que les intervenants ont reçu la formation et l'information adéquate au travail à réaliser.
Une seule personne - le chargé de consignation - doit être responsable
de l’exécution des opérations. La déconsignation sera effectuée par le chargé de consignation.
Le Dossier d’Interventions Ultérieures sur l’Ouvrage dans le bâtiment (DIUO)
Tout travailleur oeuvrant dans l’entretien, la maintenance dans un bâtiment ne doit intervenir qu’à partir du moment où il connaît exactement la nature des risques auxquels il est exposé.
C’est pourquoi le Code du Travail demande que la sécurité des travailleurs pendant les interventions ultérieures soit prise en compte dès la conception du bâtiment. Le DIUO (Dossier d’Interventions Ultérieures sur l’Ouvrage) est établi pour faciliter la transmission d’informations opérationnelles aux services ou prestataires (chargés de l’entretien, de la maintenance, du nettoyage…) et leurs salariés et informer les utilisateurs des moyens et des consignes à mettre en oeuvre lors des opérations de maintenance de manière à limiter les risques d’atteinte à la sécurité des opérateurs. En particulier, il décrit les dispositions organisationnelles et les moyens à préconiser lors des interventions de maintenance (équipement d’élévation du personnel, moyens de levage,..)
Cela concerne :
- le nettoyage des surfaces vitrées en élévation et en toiture ;
- l'accès en couverture, et notamment :
les moyens d'arrimage
les possibilités de mise en place de garde-corps ou de filets de protection
- l'entretien des façades et notamment les moyens d'arrimage et de stabilité d'échafaudage ou de nacelle.
- les travaux d'entretien intérieur et notamment pour :
le ravalement des halls de grande hauteur,
les accès aux cabines d'ascenseurs,
les accès aux canalisations en galerie technique ou en vide sanitaire,
- les entretiens des équipements, machines, réseaux … (ascenseurs, fermetures automatiques, chauffage ventilation et climatisation, tableaux électriques etc.)
Prévention des principaux risques
La maintenance et l’entretien des équipements apportent des risques supplémentaires à ceux de la production normale qu’il convient de bien appréhender en amont des travaux pour éviter tout incident ou accident : électrocution, projections, inhalation de substances toxiques, mais aussi simplement chutes…
Les principaux risques sont notamment :
- conditions de travail contraignantes dues en particulier aux manutentions manuelles et
aux postures du travail dans un espace souvent restreint, facteur de l’apparition de nombreux troubles musculo-squelettiques (TMS) : utiliser au maximum des aides à la manutention et proposer une formation PRAP (Prévention des Risques liés à l'Activité Physique) - chute de plain-pied résultant de glissade, faux pas et trébuchement, chute dans un escalier : il convient de bien éclairer et d’entretenir les sols des locaux techniques et leurs escaliers d’accès et les munir de dispositifs anti-dérapants.
- machines en mouvement, bris d’outils coupants, facteur d’écrasements, de coupures multiples : mettre des carters de protection, arrêt d'urgence, consignation
- pièces nues sous tension, effets du courant électrique : habilitation électrique, cadenas et étiquettes de consignation
- travail en hauteur, facteur de chutes : fournir des escabeaux conformes et proscrire l'usage des échelles mobiles
- les risques hydrauliques et oléo-hydrauliques liés à la pression, à la température, lors du contrôle, du démontage avec les risques d'éclatement, de rupture de tuyauteries rigides ou flexibles avec fouettement et projection : dispositifs de verrouillage, consignation
- exigence des clients : charge mentale liée aux délais générant souffrance psychique, facteur de stress : former au « coping » face à une personne agressive, veiller à la gestion des volumes de travail
Partagez et diffusez ce dossier
Laissez un commentaire
Votre adresse de messagerie ne sera pas publiée.