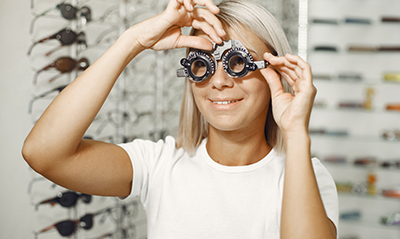
L'industrie automobile est l'un des secteurs manufacturiers les plus importants, avec un poids économique considérable et est soumise à une forte intensité concurrentielle. L'industrie automobile est un domaine très vaste, depuis la fabrication des pièces du moteur, de la carrosserie, des selleries, des garnitures et tableaux de bord, de l'électronique embarquée, jusqu'à l'assemblage final du véhicule : de nombreux métiers sont concernés par des risques professionnels ...
L'industrie automobile est l'un des secteurs manufacturiers les plus importants, avec un poids économique considérable et est soumise à une forte intensité concurrentielle. L'industrie automobile est un domaine très vaste, depuis la fabrication des pièces du moteur, de la carrosserie, des selleries, des garnitures et tableaux de bord, de l'électronique embarquée, jusqu'à l'assemblage final du véhicule : de nombreux métiers sont concernés par des risques professionnels physiques et chimiques, à la fonderie, au forgeage, à l'emboutissage, à l'usinage et au traitement de surface des pièces détachées, à la peinture, au montage du châssis …
Les cadences élevées de production des travailleurs des constructeurs d'automobiles, de leurs équipementiers et de leurs très nombreux sous-traitants, la présence d'un effectif d'ouvriers intérimaires important, le travail en flux tendus et posté en équipes alternantes, ont tendance à augmenter la fréquence des accidents du travail : chutes de plain-pied, troubles musculo-squelettiques, coupures et contusions diverses notamment liées à l'utilisation des machines-outils et des robots industriels, projections oculaires, troubles auditifs, intoxications respiratoires et irritations cutanées dues aux solvants, lubrifiants, adhésifs, acides utilisés.
De plus, les gains de productivité exigés exercent une pression constante sur les conditions de travail de tout le personnel de l'industrie automobile, même dans les bureaux d'études, les services des achats, … ou l'apparition de troubles psychosociaux est fréquent du fait du stress au travail.
Les risques physiques et chimiques des ateliers de l'industrie automobile peuvent être maîtrisés par l'utilisation de machines et d'équipements conformes aux normes, avec des dispositifs de protection et de signalisation et des barrières physiques et immatérielles, la captation de gaz et de poussières au plus près de leur point d'émission, une ventilation efficace, et par le respect des exigences essentielles de sécurité (lutte contre le bruit, hygiène des locaux…) et de protection individuelle, avec une attention soutenue pendant les périodes de mise en place des outillages et de démarrage de production, ou lors des opérations de maintenance et de réparation des chaines de fabrication.
La prévention du stress et des atteintes à la santé mentale liées à l'intensification du rythme de travail, relève de mesures organisationnelles, principalement dans le domaine du management.
La prévention des risques professionnels dans l'industrie automobile
Il y a un grand nombre de types de véhicules (tourisme, utilitaires légers, camions, autobus et autocars, …) et de nombreuses étapes de fabrication avec des processus mis en œuvre très divers ; les risques d'accidents varient d'un atelier à l'autre de la même usine ou chez les équipementiers ou sous-traitants fournisseurs spécialisés : une ligne de montage de véhicules à moteur assemble des pièces et des composants provenant de diverses usines de fabrication.
La production automobile a été et est encore le plus souvent à la pointe de l'innovation en matière de process industriel et d'organisation du travail (du « fordisme » au « toyotisme ») : le taylorisme, l'organisation scientifique du travail, les flux tendus et le «juste-à-temps», le lean manufacturing, la robotisation industrielle, … sont nées de la recherche permanente de productivité au sein de fabrications de grande séries, avec des cadences élevées de production et des exigences fortes de qualité et de sécurité des produits.
La pénibilité des métiers de l'automobile est distincte entre les sites de production des grands constructeurs et des équipementiers de rang 1, automatisés et disposant de moyens techniques importants, et les sites des équipementiers de rang 2 ou 3 ou la multitude de sous-traitants où les tâches manuelles peuvent être encore dominantes, exposant aux troubles musculo-squelettiques causés par les activités en station debout prolongée, s'effectuant avec des gestes répétitifs ...
- Les risques physiques et chimiques dans l'industrie automobile
La fonderie de métaux ferreux et d'aluminium de pièces coulées pour blocs moteurs, culasses, carters … à partir de métal en fusion exposent évidemment à un risque de brûlure thermique par projection de métal ou exposition aux rayons infrarouges. Les accidents du travail provoqués par des blessures aux mains ou des corps étrangers dans les yeux sont également très fréquents. De nombreux agents chimiques dangereux (silice cristalline, formaldéhyde, Hydrocarbures Aromatiques Polycycliques, fumées des alliages métalliques liquides, Fibres Céramiques Réfractaires…) sont utilisés ou émis lors des différents procédés de moulage en sable et noyaux qui utilisent également des résines dont la dégradation thermique pendant la coulée génèrent des substances toxiques : les affections respiratoires sont des maladies professionnelles préoccupantes pour les fondeurs, avec la possibilité d'apparition de cancers. Les niveaux sonores élevés exposent les opérateurs de fonderie aux postes de dénoyautage, de démoulage, décochage, ébarbage … à des risques de troubles auditifs, pouvant entrainer à la longue une surdité professionnelle.
L'usinage des métaux pour la fabrication de pièces détachées pour suspensions, transmissions, vilebrequins, engrenages … met en œuvre des machines à commande numérique (centre d'usinage) pour fabriquer des pièces par enlèvement de métal avec des outils coupants. Il en résulte des dangers de nature physique importants (coupures, écrasements, poussières dans l'œil…), mais également de nature chimique, à cause des huiles de coupe utilisées comme lubrifiant qui présentent des risques cutanés et respiratoires.
Le traitement des surfaces métalliques est constitué d'opérations physiques, chimiques, électrolytiques (placage) destinées à modifier leur aspect ou leurs propriétés, notamment pour augmenter la résistance à la corrosion ou à l'usure, ou pour préparer à un revêtement (dégraissage ou décapage). Le traitement de surface utilise de nombreux produits chimiques toxiques, corrosifs et cancérogènes (solvants chlorés, dérivés du chrome, cyanure, cadmium, acides et alcalins…) : des contacts cutanés et surtout l'exposition des travailleurs aux poussières nocives et aux émanations de solvants et vapeurs acides provenant des cuves de traitement dans l'air ambiant constituent des risques élevés pour la santé des travailleurs. Les opérations de peinture utilisent des solvants organiques et des liants filmogènes (résines…), des pigments, et provoquent des émissions de Composés Organiques Volatils (COV) ayant une grande toxicité en particulier neurologique et présentant des risques d'allergies cutanées et respiratoires importants.
L'emboutissage de tôles, de feuillards en bobine, pour obtenir des panneaux de carrosserie, capots, portes … s'effectue par application à température ambiante d'efforts énormes de cisaillage, compression puis par soudage éventuellement pour les sous-ensembles, dans des grandes usines équipées de presses automatiques et souvent robotisées. Ces opérations s'accompagnent de vibrations et de bruits à forte intensité impulsionnelle (plus de 100 dBA), qui engendrent un risque de déficit auditif, et de possibilités d'accidents très graves, résultant de mouvements non prévus des machines : risques de lacération, d'écrasement ou de sectionnement des membres, de happement des vêtements ou des cheveux, … Les brouillards et fumées de dégradation des graisses d'emboutissage et les fumées de soudage sont susceptibles de provoquer des pathologies respiratoires (asthme et pneumopathies).
Le forgeage, pour produire des pièces de moteur, de transmissions et de suspensions, s'effectue au moyen de billettes chauffées par induction placées sur des presses à forger ou par un forgeage à froid sur des marteaux-pilons suivi d'un traitement thermique : aux risques élevés des émissions sonores, de coupures, de projections de métal, des fumées des lubrifiants des matrices, s'ajoutent les expositions aux fortes températures et aux risques de brûlures thermiques.
La plasturgie pour la fabrication de panneaux de carrosserie moulés en polymères, de pièces de finition et de tableau de bord, des sièges et éléments de garnissage intérieur, utilisent des matières plastiques renforcées de fibre de verre, de plastiques thermodurcissables, d'acrylonitrile-styrène-butadiène ou de polyéthylène, de matériaux polyuréthanes comme les mousses pompables pour insonoriser les voitures : ils exposent les opérateurs à des risques chimiques induits soit par contact cutané, soit par voie respiratoire par inhalation de poussières ou libération de produits volatils toxiques lors de l'élévation de la température mise en œuvre dans le procédé de fabrication, avec libération de monomères ou de produits de base résiduels (formol, phénol, isocyanates, diisocyanate de toluène, styrène …). Les matières plastiques sont aussi une cause fréquente de dermatoses professionnelles avec des composants irritants et allergènes (monomères, durcisseurs et certains additifs et catalyseurs). A ces risques chimiques, s'ajoutent des risques liés à la chaleur ambiante des machines, étuves et fours de séchage, au bruit et aux vibrations des presses, concasseurs …
Les risques chimiques s'étendent à l'utilisation d'une large gamme d'adhésifs pour fixer des éléments ou pour garantir l'étanchéité de certaines pièces, de fluides caloporteurs, hydrauliques et liquides réfrigérants : beaucoup de ces produits utilisés sont corrosifs ou irritants cutanés et respiratoires, avec des dangers accentués lors de projections massives ou de déversements importants.
Les ateliers de carrosserie, de montage du châssis et d'assemblage final présentent plusieurs risques fréquents causés entre autres par une mauvaise ergonomie au poste de travail. Les TMS (troubles musculo-squelettiques) sont provoqués par les gestes répétitifs, associés à des efforts excessifs et mauvaises postures, en particulier le mal de dos (cervicalgies et lombalgies), les tendinites du poignet (syndrome carpien), du coude, ou de l'épaule, les affections des vaisseaux sanguins des jambes … On note aussi les risques de coupures aux mains ou d'écrasements lors des déplacements des éléments mobiles des machines d'assemblage, de chutes de plain-pied, de chutes d'objets, de collisions avec des chariots de manutention, d'électrisation/électrocution … La pénétration par négligence, distraction ou nécessité dans la zone d'évolution des robots, la neutralisation des protections, représente un danger majeur : même après un arrêt d'urgence, le robot peut rester dangereux du fait de son énergie résiduelle non purgée de ses composants électriques ou hydrauliques, d'un mouvement imprévu du bras. Le dysfonctionnement du système robotisé lui-même peut avoir différentes origines : défaillances ou pannes ou modifications hasardeuses des moyens de protection, défaillances du système électronique de commande, du logiciel, mauvaise disposition des protecteurs ou la mauvaise réaction à une situation anormale. Les dangers peuvent survenir lors de l'utilisation du robot mais aussi et surtout lors de sa maintenance ou de son réglage : risques mécaniques élevés de collision avec l'utilisateur, du fait notamment de la vitesse élevée d'exécution, du manque ou de la difficulté d'anticipation de certains mouvements des parties mobiles, de la force des impacts. - Les risques psychologiques dans l'industrie automobile
Les gains de productivité exercent une pression constante sur les conditions de travail des travailleurs des constructeurs d'automobiles et de leurs équipementiers à la fois dans les usines mais aussi dans les bureaux d'études, des achats, de marketing, de promotion des ventes … ou la sortie de nouveaux modèles de plus en plus performants et la réduction du « time to market » est un impératif sans cesse renouvelé.
Le stress permanent a des effets destructeurs et pathogènes sur les individus qui y sont soumis, mais les troubles comportementaux qui en résultent rejaillissent également sur toute la structure entrepreneuriale.
La confirmation de la réalité croissante des atteintes à la santé psychique et de ses effets somatiques par le stress (maladies cardio-vasculaires, troubles musculo-squelettiques, troubles gastro-intestinaux, états d'anxiété et dépressifs…) et du rôle des facteurs organisationnels dans l'industrie automobile constitue une alerte majeure de santé au travail pour ces entreprises.
Différentes méthodes de gestion industrielle, regroupées sous le terme de « Lean Manufacturing » ou « gestion de production au plus juste », apparues au Japon puis théorisées et complétés aux Etats-Unis dans les années 80, sont apparues dans les processus de fabrication de grands groupes industriels de l'automobile à la fin du XXème siècle, puis se sont diffusées plus largement chez les équipementiers.
Le Lean Manufacturing, par lui-même, produit une intensification du travail, des sur-sollicitations physiques par élimination des temps d'attente et des déplacements jugés inutiles, alors que bien souvent ils permettent une récupération physique, et des contraintes cognitives par augmentation du nombre de tâches mentales. La pression sur les opérateurs pour traiter les aléas en urgence, pour augmenter la flexibilité de la production crée de plus des situations stressantes.
Augmentation de la productivité par réduction des couts et des délais et amélioration de la satisfaction au travail par développement de l'autonomie et de la participation du personnel, le Lean Manufacturing, développé initialement dans le Toyota Production System (TPS), peut aussi détériorer les conditions de travail si elles sont mal mises en œuvre, appliquées de manière directive, sans concertation, par un changement brutal : l'intensification du rythme de travail et de charge mentale sans réelles marges de manœuvre aboutit alors à une recrudescence de troubles musculo-squelettiques et de risques psychosociaux.
Néanmoins, une organisation de type toyotiste, qui laisse plus de place à l'initiative et à la participation, peut permettre à l'opérateur de devenir satisfait de son travail alors d'une organisation qui ne permet aucune marge de manœuvre (de type taylorienne) va interdire toute adaptation et laisser insatisfait ou malheureux le travailleur.
Les mesures préventives des risques professionnels dans l'industrie automobile
Les opérations dans l'industrie automobile sont aujourd'hui pour une large part automatisées et mécanisées. Le process des grandes usines ainsi fortement modernisé, robotisé, permet de réduire l'exposition des travailleurs et de diminuer considérablement les risques physiques et chimiques. Le process piloté par un contrôle informatisé centralisé réduit les interventions dans les ateliers et minore ainsi beaucoup les possibilités de sources d'exposition chimique et physique. Toutefois, des incidents dans l'automatisation des opérations, des fuites, des dysfonctionnements des asservissements… génèrent des dangers et nécessitent également des interventions de maintenance qui restent dangereuses. Par ailleurs, dans les petites usines dans lesquelles les volumes traités sont bien inférieurs, les pratiques sécuritaires sont beaucoup moins mises en œuvre et maîtrisées.
La prévention la plus efficace est la prévention primaire avec la mise en place de technologies qui permettent des actions sur les produits (suppression ou emploi de produits de substitution de moindre impact potentiel sur l'homme) et/ou des actions sur les procédés (emploi de matériels ou de machines supprimant ou limitant au maximum les impacts, par de très faibles rejets atmosphériques, par de bas niveaux sonores…).
Les moyens de prévention à mettre en œuvre pour pallier les risques professionnels dans ces usines résident ensuite dans la prévention collective (ventilation efficace de l'atelier et aspiration à la source des poussières et fumées, stockage des produits chimiques et installation électrique et de protection incendie conformes aux normes, respect des règles générales d'hygiène…) qui diminue fortement les expositions et la fréquence ces accidents, puis dans la prévention individuelle (équipements de protection) qui en diminue nettement la gravité, enfin dans la l'information et la formation à la sécurité des travailleurs.
Par ailleurs, une surveillance médicale renforcée est obligatoire pour les salariés exposés aux risques chimiques.
Les ateliers de l'industrie automobile doivent faire l'objet d'une analyse poussée des risques pour permettre la rédaction du Document Unique de Sécurité en appréciant à la fois l'environnement matériel et technique (outils, machines, produits utilisés) et l'efficacité des moyens de protection existants et de leur utilisation selon les postes de travail.
Les analyses de risques sont confiées à des spécialistes de la sécurité au travail (hygiéniste, ingénieur sécurité). Les rapports d'intervention et de maintenance seront aussi intégrés à la documentation de sécurité au travail de l'entreprise et communiquées au médecin du travail et au CHSCT.
- Une ventilation des lieux de travail adéquate
La ventilation et l'aération des lieux de travail jouent un rôle essentiel pour limiter la concentration de l'ensemble des vapeurs dans l'air ambiant et les évacuer des lieux de travail, de façon à respecter les valeurs limites fixées par les réglementations et éviter ainsi les conséquences sur la santé des travailleurs. On procède par ventilation générale des ateliers et par aspiration continue à la source aux postes de travail.
La ventilation mécanique générale, extracteur d'air pour l'aspiration des vapeurs, doit assurer un renouvellement d'air en permanence afin de limiter les risques pour la santé, en évitant l'accumulation de vapeurs nocives et explosives, par extraction et soufflage : l'air est transporté dans le local par un ventilateur de soufflage et extrait du local par un ventilateur d'évacuation. L'extraction de l'air se fait grâce à un système de collecte par ces ventilateurs et des gaines de diffusion, réseau de conduits jusqu'aux filtres et aux épurateurs dans l'installation d'air soufflé qui permettent de nettoyer l'air, puis de l'évacuer à l'extérieur par rejet dans l'atmosphère.
Les composants aérauliques comme les ventilateurs, les conduits doivent être accessibles et faciles d'entretien et de nettoyage. En particulier, les réseaux s'encrassent rapidement avec de filtres hors d'usage, une évacuation des condensats obstruée… L'entretien régulier du système de ventilation (nettoyage des conduits d'extraction, changement des filtres) est une condition indispensable de bon fonctionnement.
Ces dispositifs doivent être complétés par une ventilation avec extraction localisée des vapeurs, des fumées et particules métalliques, brouillards d'huile … avec filtres, épurateurs ou autres collecteurs de poussières.
Pour mesurer l'efficacité des installations de ventilation, la mesure périodique des agents chimiques par prélèvements d'atmosphère et analyses des vapeurs, gaz, poussières est importante.
La valeur limite correspond à sa concentration dans l'atmosphère dans laquelle une personne peut travailler pendant un temps donné sans risque d'altération pour sa santé.
La Valeur Limite d'Exposition (VLE) est la concentration maximum à laquelle un travailleur peut être exposée au plus pendant 15 mn sans altérations physiologiques : ce critère a pour but d'éviter les effets immédiats sur l'organisme. La Valeur Limite Moyenne d'exposition (VME) est la limite d'exposition d'un travailleur pour une exposition régulière de 8h par jour et de 40h par semaine : ce critère a pour objectif d'éviter les effets à long terme sur l'organisme.
La norme EN 481 concerne l'échantillonnage de poussières ou d'aérosols sur les lieux de travail et donne les caractéristiques des instruments à utiliser pour déterminer les concentrations.
Les mesures et analyses peuvent être faites par l'employeur ou par un laboratoire extérieur et le respect des valeurs limites doit être vérifié au moins annuellement.
Si la valeur limite d'exposition est dépassée, cela permet d'imposer un arrêt temporaire d'activité pour remédier à la situation, puis il faut réaliser un nouveau contrôle sans délai.
Ces rapports d'analyses métrologiques, d'intervention et de maintenance seront intégrés à la documentation de sécurité au travail de l'entreprise (Document Unique de Sécurité). - L'utilisation de machines et équipements adaptés
Toute machine doit porter les avertissements, signalisations et dispositifs d'alerte indispensables pour assurer la sécurité des travailleurs afin de supprimer ou réduire au minimum les risques de coupure, d'entraînement, d'écrasement, de cisaillement. Cette identification doit être réalisées par des pictogrammes et couleurs normalisées. Les éléments de travail doivent être disposés, protégés, commandés ou équipés de façon telle que les opérateurs ne puissent atteindre la zone dangereuse (carters de protection ou cage pour les organes en mouvement, barrages immatériels avec détection à faisceaux optiques pour presse …).
Chaque machine doit être munie de :
- Dispositifs d'arrêt d'urgence (boutons, câbles, barres) interrompant l'alimentation en énergie des actionneurs de façon sûre, clairement identifiables, accessibles et en nombre suffisant, permettant d'éviter les situations dangereuses en train de se produire.
- Ecrans de protection et de sécurité des opérateurs : protecteurs (cage, carter, couvercle, écran, porte, …) fixés à l'aide de moyens imposant un outil pour leur démontage ou par des protecteurs mobiles (enceintes…) associés à un dispositif de verrouillage : tant que le protecteur n'est pas fermé, la machine ne peut pas fonctionner. Avec un dispositif d'inter-verrouillage, le protecteur ne peut être ouvert tant que les fonctions dangereuses de la machine sont actives.
- Interrupteurs et relais de sécurité.
- Barrières immatérielles de sécurité : des dispositifs électro-sensibles de détection de présence et /ou de mouvement verrouillent les mouvements des parties mobiles pendant la présence d'un opérateur, comme des barres sensibles ou des protections à capteurs photoélectriques.
Protéger l'utilisateur du danger potentiel du robot en mouvement nécessite de créer une zone protégée par une enceinte de protection avec un accès restreint et de former aux risques et aux consignes de sécurité des systèmes robotisés : afin d'encadrer la coopération homme-machine, notamment au plan de la sécurité des opérateurs, il existe la norme ISO 10218 (août 2011), qui spécifie les exigences en matière de sécurité, d'ergonomie, de performance des « robots pour environnements industriels ».
La vérification de la mise en place, du bon état de la fonctionnement des protecteurs, des dispositifs de verrouillage ou d'inter-verrouillage et dispositifs de protection (arrêt d'urgence…) est fondamentale, pour assurer par exemple les consignes d'arrêt obligatoire, notamment lors des incidents et des opérations de maintenance, pour lesquelles une véritable procédure de consignation et déconsignation doit être mise en œuvre : en particulier, le cadenassage fait appel à des dispositifs d'isolation tels que les coupe-circuit, les cadenas et systèmes de cadenassage à distance.
Les panneaux de signalisation seront choisis et disposés de façon à être perçus et compris facilement sans ambiguïté. Les machines et équipements doivent être conçues et fabriquées de façon à ce que les émissions sonores soient réduites au niveau le plus bas possible en application d'une directive européenne 2003/10/CE du 6 février 2003 concernant les prescriptions minimales de sécurité et de santé relatives à l'exposition des travailleurs aux risques dus aux agents physiques liés au bruit.
Par le choix ou l'achat de machines et par l'utilisation de procédés silencieux, les émissions sonores peuvent être maintenues à un bas niveau.
Les machines bruyantes doivent être munies de capots insonorisants et pour réduire les bruits transmis par les sols et les structures, des blocs anti-vibrations peuvent être placés entre la machine et la surface d'appui. En ce qui concerne les locaux, les réflexions sur les murs entraînent une augmentation du niveau sonore dans le local et des mesures préventives de correction acoustique comme la mise en place d'un plafond ou faux-plafond absorbant, de cloisons amovibles recouvertes de produit anti-réverbérant à proximité des installations, réduisent à la fois le niveau sonore et protègent les postes de travail avoisinants.
Le respect des recommandations des constructeurs et un entretien régulier des installations sont des éléments essentiels pour limiter les risques accidentels et pour prévenir des émanations. Ainsi, l'utilisation et l'entretien des machines doivent être effectués par un personnel qualifié, spécifiquement formé.
Des machines utilisées de manière non conforme ou mal entretenues et non vérifiées périodiquement créent un risque supplémentaire : par exemple, protecteurs détériorés, système de freinage usé, fuites sur les circuits hydrauliques… - Une installation électrique conforme
L'incendie peut provenir des équipements électriques, et en particulier, l'équipotentialité et la bonne mise à la terre de toutes les installations métalliques doivent être contrôlées, les prises défectueuses remplacées, il faut éviter toute accumulation d'électricité statique. Les étincelles, arcs et échauffements provoqués par les moteurs et appareillages électriques en fonctionnement peuvent aussi déclencher la catastrophe. Un grand nombre de précautions doivent être prises au niveau de l'installation électrique, du branchement et de l'entretien des différents équipements (permanence de la mise à la terre, câble de masse des pièces métalliques).
Une métallisation au moyen d'un matériel conducteur et une mise à la terre appropriées de tout l'équipement sont nécessaires pour dissiper et diriger à la terre en toute sécurité les charges électriques accumulées. La protection contre les contacts avec les masses mises accidentellement sous tension est obtenue par un dispositif de coupure automatique en cas de défaut d'isolement.
Les installations électriques doivent être conformes aux normes de sécurité et périodiquement vérifiées: mise à la terre, protection contre les contacts avec les masses mises accidentellement sous tension par un dispositif de coupure automatique en cas de défaut d'isolement et utilisation de disjoncteurs différentiels de grande sensibilité… la protection contre l'électrisation est indispensable. Le travail ne doit pas s'effectuer sur un sol humide. - Une bonne tenue des locaux
Une bonne tenue des locaux est essentielle pour éviter l'accumulation de déversements et de poussières sous ou autour des machines. Les fuites et déversements peuvent créer un danger de glissement et par conséquent doivent être nettoyés et immédiatement épongé avec des absorbants. Des sols exempts de trous ou d'aspérités, avec des revêtements antidérapants, un drainage satisfaisant et des caillebotis évitent le dépôt de liquides, diminuent les risques de glissades et chutes de plain-pied.
La circulation est à l'origine de nombreux accidents ; à ce titre, le balisage, l'éclairage et la sécurisation des voies de circulation et des zones de stockage sont essentielles ainsi que le rangement en permanence et l'entretien des sols assurent la prévention des risques de chutes et de heurts.
- Pour la prévention des risques de chute de plain-pied, des revêtements de sol antidérapants doivent être privilégiés, les inégalités de surfaces et/ou obstacles doivent être soit supprimés (bouchage des trous) soit clairement signalés, notamment dans les lieux de passage.
- Il faut veiller à maintenir l'atelier rangé. Les voies de circulation doivent être débarrassées de tout obstacle. Il faut éviter les zones d'ombre en optimisant l'éclairage et signaler les escaliers, les dénivelés, les encombrements temporaires, et prévoir des aires de rangement pour les organes démontés, les pièces en attente de remontage.
- Les allées de circulation (piétons/véhicules) doivent être nettement délimitées par un marquage au sol et de largeur suffisante. Les endroits pouvant présenter un risque de danger (croisements, rétrécissements...) doivent être très nettement signalés. - Des aides à la manutention
Les nombreuses manutentions manuelles de charges lourdes qui entraînent des risques évidents de troubles musculo-squelettiques au niveau du dos et des articulations, peuvent être réduits par l'utilisation systématique de manutention assistée et de moyens de mise à niveau et de préhension des charges : ponts roulants, chariots, moyens de levage appropriés tels que palans… - Un stockage des produits chimiques rigoureux
Le stockage des produits chimiques présente des risques tels que l'incendie, l'explosion, le risque de chute ou de renversement ou de détérioration d'emballage … Toutes ces caractéristiques rendent nécessaire, outre les précautions lors de leur emploi, l'aménagement de locaux de stockage, avec des rayonnages métalliques, des planchers et des palettes normalisées, des armoires de sécurité pour petites quantités pour le stockage de produits inflammables, armoires avec étagères de rétention, matériels de stockage avec bacs rétention pour prévenir et maîtriser les fuites accidentelles de liquides polluants. La réduction des risques existants passe par une réflexion sur la structure du local, sur les modalités de rangement et sur les incompatibilités entre les produits. Des procédures de stockage non adaptées peuvent entraîner une fragilisation des emballages à l'origine de fuites ou de ruptures accidentelles, de pollution, de réactions dangereuses ou d'accidents ou induire une modification ou une dégradation des produits qui le rendent plus dangereux car ils peuvent libérer des vapeurs inflammables ou nocives.
L'empilement doit être stable et sa hauteur ne doit pas affecter l'intégrité des emballages.
Le stockage des bidons de solvants, des bouteilles de gaz, …doit se faire dans un local ventilé par un système de ventilation mécanique, à l'abri de la chaleur et de l'humidité, et tous les conteneurs de produits chimiques doivent toujours être bien refermés.
L'installation électrique du local de stockage est à réaliser avec du matériel utilisable en atmosphère explosible. Une bonne tenue des sols, imperméables et incombustibles, des locaux de stockage est essentielle pour éviter l'accumulation des matières déversées.
L'interdiction de fumer dans les locaux doit être absolument respectée et signalée de manière apparente (de même que toutes les autres consignes de sécurité).
Il faut stocker les plus faibles quantités de produits possibles car le risque d'incident ou d'accident croît avec la durée et le volume de stockage.
Il faut régulièrement vérifier les zones de stockage des produits chimiques utilisés dans les procédés, afin de repérer les fuites éventuelles. - Le respect des règles d'hygiène et de sécurité
Une bonne tenue des sols des locaux par aspiration ou par un procédé à l'humide (jet d'eau ou système eau/vapeur), est essentielle pour éviter l'accumulation de déversements et de poussières sous ou autour des machines. Les déversements peuvent créer un danger de glissement et par conséquent doivent être nettoyés immédiatement. Des mesures complémentaires d'hygiène des locaux doivent être mises en œuvre tel le nettoyage régulier des machines et des parois de l'atelier à l'aide d'un aspirateur industriel adapté avec un filtre absolu qui ne disperse pas les poussières dans l'air (pas de soufflette à l'air comprimé, ni balayage).
Des lavabos, postes de rinçage oculaire et des douches de sécurité doivent se trouver à proximité des postes de travail. Celles-ci permettent les mesures d'hygiène générale : lavage des mains fréquent avec moyens adaptés, douche en fin de poste... En effet, le respect des règles d'hygiène s'étend aux comportements individuels : ne pas avoir les mains sales afin de ne pas ingérer par inadvertance un produit toxique et ne pas manger sur le lieu de travail. Le personnel doit avoir à sa disposition des vestiaires et des sanitaires correctement équipés et en nombre suffisant. Des vestiaires doubles doivent être mis à la disposition des travailleurs : l'entreposage des tenues de travail doit avoir lieu à l'abri de la poussière et des souillures (le rangement des tenues de ville et des tenues de travail doit être séparé).
Les consignes en cas d'accident (n° d'appel d'urgence, conduite à tenir, identification des services de secours) doivent être visiblement affichées.
Une trousse contenant le matériel de premiers secours non périmé doit être mise à la disposition du personnel, toute blessure cutanée doit immédiatement être désinfectée et pansée.
Les projections de poussières ou autres corps étrangers dans les yeux doivent être immédiatement ôtées avec un rinçage oculaire.
Des extincteurs doivent être disponibles en nombre suffisant et vérifiés annuellement. - Le port d'équipements de protection individuel adéquat
Les équipements de protection individuelle sont nécessaires pour réduire le risque d'exposition non totalement éliminé par les mesures de protection collectives précédentes : gants, vêtements de protection, chaussures et lunettes de sécurité, écran facial de protection, coquilles ou bouchons d'oreille contre le bruit…Ils doivent être différents et adaptés à la tâche effectuée.
S'il y a possibilité de contact avec la main lors des transvasements de produits chimiques par exemple, il s'avère indispensable de porter des gants de protection adaptés au produit manipulé : il n'existe pas de gant de protection universel. Le type de gants conseillé, imperméables, à longues manchettes, pour éviter la pénétration des produits à l'intérieur, doit être adapté aux différents produits manipulés selon leur composition qui figure sur la Fiche de Sécurité (FDS). Des gants appropriés doivent être aussi utilisés pour éviter les coupures aux mains.
En cas d'urgence ou pour des travaux exceptionnels d'entretien de courte durée, si le système de ventilation ne suffit pas à empêcher l'accumulation de vapeurs ou de poussières, un appareil de protection respiratoire adéquat doit être fourni pour éviter l'exposition à une concentration élevée : masques respiratoires filtrants de type FFP2 ou masque à cartouche FFP3 avec un filtre adapté au produit, selon les concentrations.
De même, des protections auditives peuvent être nécessaires pour compléter les mesures collectives qui s'avéreraient insuffisamment efficaces. - La surveillance médicale
Pour les travailleurs exposés aux poussières de métaux, aux agents cancérogènes, au bruit, et travaillant de nuit, il faut réaliser des visites médicales régulières dans le cadre d'une surveillance médicale renforcée :
- Tests respiratoires (spiromètre) à l'embauche pour détecter une déficience des fonctions pulmonaires et tous les 2 ans pour dépister l'apparition des troubles respiratoires.
- Radiographie thoracique si nécessaire, épreuves fonctionnelles respiratoires (EFR) conseillées,
- Audiogramme si nécessaire.
- Vaccination antitétanique tous les dix ans - La prévention des risques liés au Lean Manufacturing passe par une démarche ergonomique préalable et continue, une conduite du changement et une modification et adaptation profonde des styles de management.
Il convient de disposer d'assez de personnes compétentes en organisation du travail pour traiter les problèmes remontés de la base, et d'associer les méthodistes, les ergonomes et la médecine du travail pour éviter les erreurs et utiliser leur possibilité d'intervention experte. L'adaptation des nouveaux modes opératoires aux différentes morphologies et capacités selon l'âge sont particulièrement à prendre en compte.
Il faut éviter que la quantification de toutes les tâches (chronométrage) n'aboutisse à la suppression intégrale de tous les moments d'échanges et de déplacements nécessaires au lien social et que les outils d'autocontrôle conduisent à un plus grand isolement du travailleur.
Le Lean Management ne peut avoir de succès que lorsqu'il s'insère dans une culture d'entreprise prête à une telle transformation : l'état d'esprit et les comportements des managers disposés à laisser leurs subordonnés s'exprimer et prendre des initiatives, leur qualité d'écoute, un climat de travail sain et pas seulement court-termiste sont indispensables pour un tel changement d'envergure. A défaut, il faut envisager de renouveler les structures hiérarchiques trop autoritaires, strictement attachées aux décisions par voie descendante (top-down) et totalement rétives à l'inverse (bottom-up). - La prévention des risques du stress au travail
Les actions de prévention sont complexes à concevoir et lourdes à mettre en œuvre, mais d'abord il faut acquérir les connaissances et capacités à combiner les schémas explicatifs des phénomènes.
Repérer les indicateurs d'alerte de souffrance au travail chez les salariés :
augmentation de la fréquence et de la gravité des urgences sur le lieu du travail liées à des incidents conflictuels (actes de violence, bouffées délirantes, tentative de suicide …), de l'aggravation des indicateurs de santé négatifs (TMS - troubles cardio-vasculaires, dépression …), hausse du taux d 'absentéisme, du turn-over.
Avoir une démarche d'analyse des symptômes, repérer les déterminants pour remonter aux causes organisationnelles et ne pas adopter une attitude de déni : mise en évidence des situations qui dépassent les capacités d'adaptation des individus, recherche objective d'un facteur psychologique ou sociologique ou économique auquel est associé, de façon significative et importante, un certain nombre de problèmes de santé mentale.
Le CHSCT peut proposer d'effectuer une enquête de psycho-dynamique du travail auprès du personnel pour étudier les déterminants de la souffrance générée par le travail lorsque les symptômes apparaissent au vu des indicateurs d'alerte. - La formation et l'information du personnel
La formation, par un organisme agréé, sur les dangers des produits utilisés et sur les moyens de se protéger, est indispensable : par exemple, comprendre les étiquettes du contenant des produits, informer sur le risque potentiel de maladies pulmonaires et sur les moyens de les prévenir, connaître l'attitude à adopter en cas de fuite ou de déversement accidentel, savoir utiliser les E.P.I adéquats, formation aux premiers secours et incendie, formation PRAP (Prévention des Risques liés à l'Activité Physique), certificat d'aptitude à la conduite en sécurité CACES (chariot automoteur, pont roulant)… - Autres mesures de prévention spécifiques des risques de la fonderie et du forgeage
Des vêtements ignifugés de protection contre la chaleur, tablier, lunettes de sécurité avec verres filtrant les infrarouges ou écran facial de protection complètent la protection pour les travailleurs exposés à la chaleur. Des procédures de travail en ambiance chaude doivent être édictées et respectées de manière à réduire la contrainte thermique : absorption en quantité suffisante d'eau et de boissons renfermant des sels minéraux, rythme travail-repos aménagés en zone tempérée. - Autres mesures de prévention spécifiques des risques de l'usinage des métaux
Les moyens de prévention des risques chimiques doivent correspondre aux principaux risques qui sont relatifs au contact cutané avec les fluides d'usinage et à l'inhalation des brouillards d'huile.
- Aspiration, captage à la source des fumées, capotage des machines, vérification des débits d'huile (au minimum efficace pour réduire les risques d'éclaboussures).
- Eviter le contact avec les pièces, les parties des machines ou vêtements recouverts d'huile : utiliser des gants couvrant les avant-bras et des tabliers de protection, se laver les mains fréquemment.
- utiliser un produit détergent et aseptisant avant la mise en place de fluide aqueux, une eau propre de bonne qualité biologique, contrôler le niveau de pH, la teneur en micro-organismes des fluides en service.
- renouveler souvent l'huile de coupe - Autres mesures de prévention spécifiques des risques du traitement de surface des métaux
La suppression des produits les plus toxiques et leur remplacement par une technologie propre (nouveaux procédés) ou leur substitution par des produits beaucoup moins toxiques apparaissent comme des solutions prioritaires. Toutefois, cette substitution n'est envisageable que lorsqu'il existe un produit aussi efficace, tout en ne présentant pas par ailleurs d'autres risques, et lorsque c'est techniquement possible.
Par exemple, substituer pour un certain nombre d'applications :
- des solvants organiques par des produits lessiviels,
- des bains cyanurés par des bains alcalins,
- du chrome hexavalent par du chrome trivalent,
- de l'acide fluorhydrique,
- du sable par de la grenaille d'acier ou d'autres produits abrasifs non siliceux (microbilles plastique) pour le décapage par projection sous pression,
- etc. …
En général, il convient d'utiliser les produits les moins volatils et limiter la formation de poussières en privilégiant les formes de produits en pâte ou en solution, plutôt qu'en poudre.
Le respect des recommandations des constructeurs et un entretien régulier des cuves de traitement (sondes, arrivée/départ fluide, système aspiration, cuvette de rétention, couvercle…) sont des éléments essentiels pour limiter les risques accidentels et pour prévenir des émanations.
Il convient de limiter au strict minimum le nombre de travailleurs soumis au risque en restreignant l'accès des zones où se déroulent les activités et limiter la durée de travail de ces personnes dans les zones à risque et recouvrir les bains en dehors des opérations. - Autres mesures de prévention spécifiques des risques de la plasturgie
- Dispositifs de sécurité des machines : Machines fermées avec chambre de travail étanche.
- Systèmes d'encoffrement et de captage au plus près des émissions, de façon à évacuer les aérosols et les vapeurs : Il convient de doter les installations de captages localisés et avoir des dispositifs de captage au dessus de l'ensemble des équipements (hottes aspirantes, plafonds filtrants …), en particulier au niveau des moules lors de l'injection de la matière plastique, afin de maintenir un niveau d'exposition inférieur aux limites réglementaires.
- Capteurs pour mesurer les températures et réguler les dispositifs de chauffage et éviter les -surchauffes productrices d'émanations de décomposition thermique dangereuses
- Capteurs pour mesurer les pressions et réguler les dispositifs mécaniques et thermiques et éviter les surpressions internes.
Pour aller plus loin :
- OFFICIEL PREVENTION : Accueil > Protections collectives - Organisation – Ergonomie > Psychologie du travail : Les risques organisationnels du Lean Management sur la santé au travail
- OFFICIEL PREVENTION : Accueil > Formation > Fiches Métier : La prévention des risques de la robotisation industrielle
Janvier 2016
Partagez et diffusez ce dossier
Laissez un commentaire
Votre adresse de messagerie ne sera pas publiée.