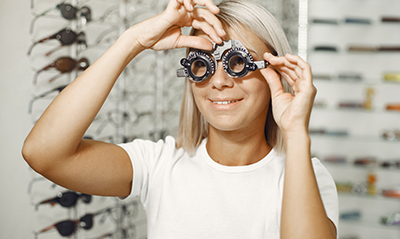
Le traitement des surfaces métalliques est constitué d'opérations physiques, chimiques, électrolytiques destinées à modifier leur aspect ou leurs propriétés. Il utilise de nombreux produits chimiques toxiques, corrosifs et cancérogènes...
Le traitement des surfaces métalliques est constitué d'opérations physiques, chimiques, électrolytiques destinées à modifier leur aspect ou leurs propriétés : décoration, résistance à la corrosion ou à l'usure, préparation à un revêtement.
Le traitement de surface utilise de nombreux produits chimiques toxiques, corrosifs et cancérogènes (solvants chlorés, dérivés du chrome, cyanure, cadmium, acides et alcalins...) : des contacts cutanés et surtout l'exposition des travailleurs aux poussières nocives et aux émanations de solvants et vapeurs acides provenant des cuves de traitement dans l'air ambiant constituent des risques élevés pour la santé des travailleurs.
Des mesures de prévention collective et individuelle sont ainsi indispensables pou permettre de réduire fortement la fréquence et la gravité des accidents du travail de traitement de surface des métaux.
La prévention consiste à :
- limiter l'utilisation des produits les plus nocifs et favoriser la substitution par d'autres qui le sont moins,
- promouvoir les installations automatiques (pompes doseuses...)
- capter les vapeurs et les aérosols par aspiration au niveau des cuves de traitement,
- utiliser des machines fermées étanches,
- ventiler les lieux de travail,
- avoir des capacités de rétention spécifiques pour recueillir les fuites et déversements accidentels,
- respecter scrupuleusement les règles de stockage des produits chimiques,
- adapter toutes les installations électriques des locaux à la zone de risque, conformément aux directives européennes ATEX concernant les atmosphères explosives,
- porter des vêtements, gants, bottes, lunettes de protection adaptés à la tâche effectuée et au produit concerné, et en cas d'urgence ou pour des travaux exceptionnels de courte durée, porter un masque de protection respiratoire,
- ...
Les informations des travailleurs exposés sur les risques des produits utilisés dans les métiers de traitement de surface, leur formation aux mesures de prévention adéquates, un suivi médical renforcé et une traçabilité de leur exposition professionnelle complètent le dispositif de sécurité au travail.
Les principaux risques professionnels du traitement de surface des métaux
Les risques des opérations de traitement des surfaces métalliques sont présents dans les trois phases du process industriel : préparation de l'état de surface par dégraissage et décapage, application d'un revêtement protecteur ou de finition par un traitement électrolytique, chimique, ou thermique, nettoyage et rinçage pour ôter des pièces métalliques l'excédent de produit. De multiples produits chimiques à toxicité chronique ou aiguë sont utilisées massivement dans l'industrie de traitement de surface, qui n'est pas exempte par ailleurs de nombreux risques moins spécifiques à cette activité (manutentions de charges, bruit, chutes de plain-pied...) qui sont susceptibles de provoquer aussi de nombreuses blessures corporelles.
-
Les risques des opérations de préparation
L'élimination des traces de graisses, huiles, de produits d'oxydation (rouille, calamine..) ou autres corps étrangers de la surface des métaux à traiter, s'opère par des procédés physiques ou chimiques présentant tous des dangers importants :
- Procédés physiques : décapage par projection abrasive par grenaillage (billes d'acier, ou microbilles de plastique, corindon), sablage ou par ultrasons. Les opérations de grenaillage et de sablage, sont à l'origine d'expositions aux poussières. Lorsque des particules de poussière irritantes se logent dans le nez, elles peuvent causer une rhinite allergique ou une inflammation de la muqueuse nasale. Certaines particules très fines réussissent à traverser la cavité nasale et à s'attaquer à la trachée et aux poumons, ou elles engendrent une inflammation des muqueuses de la trachée (trachéite) ou des bronches (bronchite). Les poumons constamment exposés à la poussière peuvent être atteint par une affection appelée fibrose (silicose pour les poussières de sable ...), entraînant des troubles respiratoires progressifs, puis irréversibles.
Les bains à ultrasons (bacs, cuves) sont utilisés pour le nettoyage et conviennent spécialement des petites pièces métalliques compliquées. Des pertes d'audition, migraines, nausées, vertiges peuvent survenir suite à l'exposition prolongée et intense aux ultrasons, particulièrement pour les personnes à l'ouïe très fine, notamment chez les jeunes travailleurs. La main peut être est soumise à une forte vibration lors d'un contact avec la source d'ultrasons (sonotrode ou pénétration de la main dans le bain).
- Procédés chimiques : dégraissage à l'aide de solvants organiques ou aqueux.
• Les solvants organiques sont soit des solvants halogénés (trichloréthylène, perchloréthylène, chlorure de méthylène..), soit des hydrocarbures avec des composants aromatiques (white spirit, toluène, xylène...)
Du fait de leur volatilité, les vapeurs se retrouvent en concentration plus ou moins élevée aux postes de travail, induisant une exposition respiratoire et parfois cutanée à de très nombreux travailleurs (en particulier, tableaux n°12 et n° 84 des maladies professionnelles du Régime Général).
Lors de l'inhalation des vapeurs des solvants, celles-ci pénètrent dans les poumons, traversent le tissu lipocutané et, par voie sanguine, se diffusent dans le corps entier et passent dans le sang, puis dans le cœur et le cerveau, avec des actions potentielles sur la moelle osseuse, et le système nerveux central : irritations des yeux et de la gorge, des organes respiratoires (asthme...), troubles cardiaques, digestifs (nausées...), du système nerveux (narcose brutale et intense pour une forte exposition), maux de tête, ...
Enfin, certains de ces solvants sont cancérigènes, possible pour le trichloréthylène, probable pour le chlorure de méthylène (ou dichlorométhane), suspecté pour le perchloréthylène (ou tétrachloréthylène) : l'exposition à ceux-ci est tout particulièrement dangereuse chez la femme enceinte car ils peuvent aussi entraîner des malformations congénitales ou perturber la grossesse et le développement du fœtus (risque tératogène et d'intoxication fœtale) en franchissant la barrière placentaire.
Les vapeurs agissent principalement par inhalation, mais les solvants organiques liquides peuvent aussi détruire le film lipidique protecteur cutané et sont donc des irritants pour la peau et les yeux, avec un pouvoir nocif variable selon les compositions chimiques.
• Les solvants aqueux sont soit composés alcalins à base de soude ou de potasse (produits lessiviels), soit des acides (chlorhydrique, sulfurique, nitrique, phosphorique ou fluorhydrique).
Tous ces produits sont hautement corrosifs par contact cutané, inhalation et ingestion : dermatoses d'irritation et brûlures profondes pour la peau, ulcérations oculaires, nasales, des voies respiratoires, et du tube digestif (dont gastrites, ulcères...).
Tableau des Maladies Professionnelles n° 32 RG. -
Les risques des opérations de déposition des métaux et galvanisation
Les revêtements s'opèrent par voie chimique par utilisation de solutions métalliques acides ou basiques (zinc, ...) ou par voie électrolytique par réactions de réduction d'un cation métallique (argenture, dorure, cadmiage, chromage, ...), ce qui confère aux pièces traitées l'aspect décoratif désiré et/ou des caractéristiques spécifiques de protection contre l'usure ou la corrosion.
On distingue :
- La galvanisation à chaud dans des bains de zinc ou d'alliage zinc-aluminium,
- La pulvérisation thermique de métal en fusion, métallisation avec du zinc, alliage zinc-aluminium ou nickel-chrome,
- L'électrolyse, traitement où les pièces sont revêtues d'un métal par dépôt électrolytique (nickelage, zingage, chromage, cadmiage...),
- L'anodisation de l'aluminium, phosphatation, nitruration, chromatation sur cuivre ou acier inox, étain, etc... qui agissent sur la modification physico-chimique de la couche superficielle de la pièce.
La multitude des produits utilisés nécessite de consulter et d'analyser les Fiches de Données de Sécurité (FDS) pour connaître les informations relatives à la toxicité de chacun d'entre eux, obligatoirement fournies par le fabricant du produit et figurant sur les étiquettes des emballages sous forme de symboles et d'informations écrites (phrases de risque R et conseils de prudence S).
On distingue les effets aigus (dus à des concentrations élevées) et chroniques (dus à de faibles concentrations, mais à des expositions répétées). Les effets aigus s'observent lors de fuites ou de déversements importants, éclaboussures ou immersions suite à des rejets accidentels massifs.
Les effets majeurs, par voie respiratoire principalement mais aussi cutanée et digestive, sont les suivants :
- Cancérogènes avérés, pulmonaires et cavités nasales : pour le chrome hexavalent libéré par l'acide chromique ou par les chromates ou bichromates (Tableaux n°10 des maladies professionnelles du RG), pour le cadmium (tableau MP 61).
- Ulcérations des muqueuses nasales et irritations pulmonaires par les brouillards acides (dont l'acide cyanhydrique) ou alcalins : brûlures sévères, perforations de la cloison nasale, broncho-pneumopathies aigues, avec atteintes systémiques possibles (atteintes rénales, gastro-intestinales, nerveuses et sanguines).
- Ulcérations oculaires, dermiques et dermites eczématiformes (allergies au nickel, tableaux MP 37...).
Les aérosols émis par les bains contenant les acides, bases et sels métalliques, les mains ou vêtements souillés d'éclaboussures de liquides ou de projections de particules, la déglutition de poussières au poste de travail sont les moyens de contamination des travailleurs de l'industrie des traitements de surface. -
Les déchets toxiques des opérations de rinçage
La phase de rinçage, destinée à ôter des pièces l'excédent de produits chimiques, engendre des déchets dangereux qui sont constitués :
- de liquides alcalins ou acides (cyanuré ou non) contenant des métaux de traitement de surface (cuivre, chrome, cadmium, zinc, nickel...),
- de boues d'hydroxyde issues du traitement des déchets liquides et des eaux de rinçage,
- de résines échangeuses d'ions saturées utilisées dans le traitement des eaux de rinçage, régénérables, ou non.
L'impact environnemental de ces polluants peut être gravissime :
- Soit par une toxicité directe immédiate, allant souvent jusqu'à la mortalité des êtres vivants dans les eaux de surface atteintes par le rejet accidentel de bains concentrés, et la pollution des eaux souterraines.
- Soit par des effets indirects et différés sur le milieu naturel, notamment pour les organismes aquatiques, dont ceux liés au risque de toxicité à long terme dû à l'accumulation de substances nocives à biodégradabilité faible.
Les mesures de prévention des risques du traitement de surface des métaux
Les installations de traitement de surface doivent faire l'objet d'une analyse poussée des risques pour permettre la rédaction du Document Unique de Sécurité (Décret du 5 novembre 2001) en appréciant à la fois l'environnement matériel et technique (outils, machines, produits utilisés) et l'efficacité des moyens de protection existants et de leur utilisation selon les postes de travail.
Les analyses de risques sont confiées à des spécialistes de la sécurité au travail (hygiéniste, ingénieur sécurité). Les rapports d'intervention et de maintenance seront aussi intégrés à la documentation de sécurité au travail de l'entreprise et communiquées au médecin du travail et au CHSCT.
Les salariés doivent être aussi informés à propos des produits dangereux mis en œuvre et formés aux pratiques professionnelles sécuritaires.
-
La métrologie des produits toxiques des traitements de surface
Pour mesurer leur capacité de toxicité, la mesure des émissions des agents chimiques volatils par prélèvements d'atmosphère et analyses des vapeurs, gaz, poussières est une étape importante pour la mise en œuvre de plans de réduction et de retrait éventuel de l'exposition.
La valeur limite correspond à sa concentration dans l'atmosphère dans laquelle une personne peut travailler pendant un temps donné sans risque d'altération pour sa santé.
La Valeur Limite d'Exposition (VLE) est la concentration maximum à laquelle un travailleur peut être exposée au plus pendant 15 mn sans altérations physiologiques : ce critère a pour but d'éviter les effets immédiats sur l'organisme.
La Valeur Limite Moyenne d'exposition (VME) est la limite d'exposition d'un travailleur pour une exposition régulière de 8h par jour et de 40h par semaine : ce critère a pour objectif d'éviter les effets à long terme sur l'organisme.
Ces valeurs limite s'expriment en "ppm" (partie par million) ou en mg par m3 :
Par exemple :
- la VLE du trichloréthylène est de 200 ppm soit 1080 mg/m3 et sa VME est de 75 ppm soit 405 mg/m3.
- La VLE du chrome hexavalent est de 0,1 mg/m3 et sa VME est de 0,05 mg/m3.
La norme EN 481 concerne l'échantillonnage de poussières ou d'aérosols sur les lieux de travail et donne les caractéristiques des instruments à utiliser pour déterminer les concentrations.
Les mesures et analyses peuvent être faites par l'employeur ou par un laboratoire extérieur et le respect des valeurs limites doit être vérifié au moins annuellement.
Si la valeur limite d'exposition est dépassée, cela permet d'imposer un arrêt temporaire d'activité pour remédier à la situation, puis il faut réaliser un nouveau contrôle sans délai.
Des détecteurs d'acide cyanhydrique permettent une action précoce pour protéger le personnel. -
La suppression / substitution des produits les plus dangereux
La prévention la plus efficace est la prévention primaire avec la mise en place de technologies qui permettent des actions sur les produits (suppression ou emploi de produits de substitution de moindre impact potentiel sur l'homme et l'environnement) et/ou des actions sur les procédés (emploi de matériels ou de machines supprimant ou limitant au maximum les impacts sur l'environnement : très faibles rejets atmosphériques et volumes de déchets et d'effluents générés les plus faibles possibles).
La suppression des produits les plus toxiques et leur remplacement par une technologie propre (nouveaux procédés) ou leur substitution par des produits beaucoup moins toxiques apparaissent comme des solutions prioritaires. Toutefois, cette substitution n'est envisageable que lorsqu'il existe un produit aussi efficace, tout en ne présentant pas par ailleurs d'autres risques, et lorsque c'est techniquement possible.
Par exemple, substituer pour un certain nombre d'applications :
- des solvants organiques par des produits lessiviels,
- des bains cyanurés par des bains alcalins,
- du chrome hexavalent par du chrome trivalent,
- de l'acide fluorhydrique,
- du sable par de la grenaille d'acier ou d'autres produits abrasifs non siliceux (microbilles plastique) pour le décapage par projection sous pression,
- etc. ...
En général, il convient d'utiliser les produits les moins volatils et limiter la formation de poussières en privilégiant les formes de produits en pâte ou en solution, plutôt qu'en poudre. -
L'utilisation de machines et équipements adaptés
- marquage des cuves et des équipements selon le système d'identification de la norme NF A 91-7016, séparation en fonction des groupes de compatibilité définis dans la norme NF A 91-701. Cela permet d'identifier chaque cuve en évitant la proximité entre deux cuves à contenant incompatible et pour éviter tout mélange accidentel avec risque de réactions explosives, de dégagement d'acide cyanhydrique...
- machines fermées avec chambre de travail étanche,
- systèmes de capot et de captage au plus près des émissions, de façon confiner le plus possible la zone d'émission des polluants (billes de plastique ou un agent mouillant à la surface des bains) et à évacuer les aérosols et les vapeurs (par exemple aspiration sur la dégraisseuse pour capter les vapeurs de perchloréthylène, ...),
- cabines de ponçage maintenues en dépression, cabines de sablage en chaudronnerie ventilée équipée d'un dispositif de récupération automatique des sables.
- cuve à ultrasons avec couvercle avec joints parfaitement adhérents et dispositif de verrouillage électrique afin d'empêcher le fonctionnement du bain avec le couvercle ouvert, revêtement acoustique interne absorbant...
- Les installations automatiques (pompes doseuses...) doivent être privilégiées, afin d'éviter les interventions manuelles pour le remplissage/vidange ou prise d'échantillon des bains.
Pour le transfert de produits dangereux, il faut éviter l'utilisation de tuyauteries flexibles et préférer l'installation d'une tuyauterie rigide et d'une pompe fixe plutôt qu'une pompe mobile.
- Des bacs de rétention spécifiques, pour le stockage des produits et pour les bains, doivent être mises en place pour recueillir les fuites et déversements accidentels.
- Des sols avec des revêtements antidérapants, un drainage satisfaisant et des caillebotis autour des bacs, pour éviter le dépôt de liquides : les sols doivent être de plus nettoyés régulièrement et tout produit accidentellement répandu, lors d'une fuite ou déversement, immédiatement épongé pour éviter les glissades et chutes de plain-pied. Il convient par ailleurs de récupérer les égouttures sur des plateaux, lors du transfert des pièces entre les bains.
Le respect des recommandations des constructeurs et un entretien régulier des cuves de traitement (sondes, arrivée/départ fluide, système aspiration, cuvette de rétention, couvercle...) sont des éléments essentiels pour limiter les risques accidentels et pour prévenir des émanations. Ainsi, l'utilisation et l'entretien des machines doivent être effectués par un personnel qualifié, spécifiquement formé.
Des machines utilisées de manière non conforme ou mal entretenues et non vérifiées périodiquement créent un risque chimique supplémentaire. -
Une ventilation des lieux de travail adéquate
La ventilation et l'aération des lieux de travail jouent un rôle essentiel pour limiter la concentration de l'ensemble des vapeurs dans l'air ambiant et les évacuer des lieux de travail, de façon à respecter les valeurs limites fixées par les réglementations et éviter ainsi les conséquences sur la santé des travailleurs.
La ventilation mécanique générale, extracteur d'air pour l'aspiration des vapeurs, doit assurer un renouvellement d'air en permanence afin de limiter les risques pour la santé, en évitant l'accumulation de vapeurs nocives et explosives, par extraction et soufflage : l'air est transporté dans le local par un ventilateur de soufflage et extrait du local par un ventilateur d'évacuation. L'extraction de l'air se fait grâce à un système de collecte par ces ventilateurs et des gaines de diffusion, réseau de conduits jusqu'aux filtres et aux épurateurs dans l'installation d'air soufflé qui permettent de nettoyer l'air, puis de l'évacuer à l'extérieur par rejet dans l'atmosphère.
Les composants aérauliques comme les ventilateurs, les conduits doivent être accessibles et faciles d'entretien et de nettoyage. En particulier, les réseaux s'encrassent rapidement avec de filtres hors d'usage, une évacuation des condensats obstruée... L'entretien régulier du système de ventilation (nettoyage des conduits d'extraction, changement des filtres) est une condition indispensable de bon fonctionnement. -
Les mesures organisationnelles de prévention
Les moyens de prévention à mettre en œuvre pour pallier les risques professionnels des traitements de surface résident aussi dans les mesures organisationnelles visant à diminuer fortement le nombre de personnes exposées et la durée et l'intensité d'exposition, par exemple en mettant des barres d'égouttage au dessus des bains pour y limiter la présence des travailleurs à proximité.
Ces mesures concernent les zones de travail, leur accès et leur balisage, les modes opératoires limitant l'importance des manipulations et les efforts physiques qui augmentent la ventilation pulmonaire donc l'inhalation des poussières et de vapeurs, par exemple en approvisionnant les produits en quantité strictement nécessaire (prépesage des produits).
Il convient de limiter au strict minimum le nombre de travailleurs soumis au risque en restreignant l'accès des zones où se déroulent les activités et limiter la durée de travail de ces personnes dans les zones à risque et recouvrir les bains en dehors des opérations. -
Un stockage des produits chimiques rigoureux
Le stockage des produits chimiques présente des risques tels que l'incendie, l'explosion, le risque de chute ou de renversement d'emballage... Toutes ces caractéristiques rendent nécessaire, outre les précautions lors de leur emploi, transport et transvasement, l'aménagement de locaux de stockage. La réduction des risques existants passe par une réflexion sur la structure du local, sur les modalités de rangement et sur les incompatibilités entre les produits. Dans le domaine du traitement de surface, plusieurs produits sont incompatibles les uns avec les autres ou correspondent à des situations d'entreposage dangereuses. Des procédures de stockage non adaptées peuvent entraîner une fragilisation des emballages à l'origine de fuites ou de ruptures accidentelles, de pollution, de réactions dangereuses ou d'accidents ou induire une modification ou une dégradation du produit qui le rend plus dangereux.
Le stockage des bidons de solvants doit se faire dans un local ventilé et sur cuvette de rétention, et toujours bien refermés.
L'interdiction de fumer dans les locaux doit être absolument respectée et signalée de manière apparente (de même que toutes les autres consignes de sécurité).
Il faut stocker les plus faibles quantités de produits possibles car le risque d'incident ou d'accident croît avec la durée et le volume de stockage.
Le sol doit être en matière ininflammable, imperméable, résistant aux produits chimiques et en légère pente vers un caniveau d'évacuation relié à une fosse de récupération.
Les produits chimiques doivent être isolés du sol. Pour cela, il est possible d'utiliser des caillebotis. Tout stockage doit être muni d'une cuvette de rétention ayant la capacité de contenir au moins le contenu du plus grand réservoir ou la moitié de la totalité des réservoirs stockés.
Il faut prévoir une réserve de matière absorbante à proximité du local : il existe des kits de dépollution à disposer dans des armoires près des zones de stockage.
Le local doit posséder un système d'extinction incendie, et une douche oculaire et un lave-œil de sécurité doivent être installés à proximité.
Les parois du local doivent être en matériaux ininflammables. -
Une installation électrique conforme
L'incendie et/ou l'explosion peuvent provenir des équipements électriques, et en particulier, l'équipotentialité et la bonne mise à la terre de toutes les installations métalliques doivent être contrôlées, les prises défectueuses remplacées, et il faut éviter toute accumulation d'électricité statique.
Les étincelles, arcs et échauffements provoqués par les moteurs et appareillages électriques en fonctionnement peuvent aussi déclencher la catastrophe.
Le but principal de l'appareillage électrique pour atmosphères dangereuses est de prévenir que le matériel, y compris l'éclairage, soit à l'origine d'un incendie ou d'une explosion.
Dans le domaine des atmosphères explosives (Atex), des normes européennes fixent le cadre de travail des industriels et des installateurs. Depuis juin 2003, tout nouveau site de type Atex doit être équipé avec du matériel certifié, avec des enveloppes antidéflagrantes. Les autres installations doivent, depuis juin 2006, avoir été mises à niveau. -
Des mesures d'hygiène
- Un nettoyage régulier permet de réduire les niveaux de poussières.
Il convient de réaliser un nettoyage des lieux de travail avec les outils appropriés, avec des précautions pour éviter la dispersion des poussières lors du vidage des aspirateurs ou des conteneurs à déchets, du changement des filtres des dépoussiéreurs.
Les zones de travail doivent être nettoyées avec un chiffon humide ou un aspirateur à filtre absolu, jamais avec une soufflette ou un balai à sec, ni avec de l'air comprimé pour éliminer les poussières adhérentes. Ces mesures d'hygiène concernent les sols et les plans de travail, mais aussi les murs et les plafonds.
- Des installations sanitaires (WC, lavabos, douches) doivent être mises à disposition des travailleurs, correctement équipées et en nombre suffisant, permettant aux travailleurs de se nettoyer fréquemment les mains et le visage à l'eau et au savon et de se laver en fin de poste pour limiter l'incrustation des particules dans la peau. En cas de forte contamination, les installations sanitaires doivent elles-mêmes faire l'objet d'un nettoyage méticuleux.
- Des douches oculaires portatives conçues pour fournir immédiatement le liquide de rinçage et des fontaines rince yeux/visage fixes doivent être disponibles.
- Des vestiaires appropriés doivent être mis à la disposition des travailleurs : l'entreposage des tenues de travail doit avoir lieu à l'abri de la poussière (le rangement des tenues de ville et des tenues de travail doit être séparé).
- La gestion et le nettoyage des vêtements de travail et autres équipements individuels de protection fournis aux travailleurs doivent être pris en charge par l'employeur.
- La trousse de secours doit contenir des produits spécifiques (gluconate de calcium en solutions injectable et buvable, ou en crème en cas d'accident avec l'acide fluorhydrique). -
Le port d'équipements de protection individuel adéquat
- En cas d'urgence ou pour des travaux exceptionnels de courte durée dans des atmosphères polluées par des émissions de vapeurs ou poussières, ou pour des concentrations attendues élevées (pendant le sablage, le grenaillage...), il est nécessaire de porter un appareil de protection respiratoire : des demi-masques, avec cartouche filtrante adaptée au produit, de type P3, prenant le nez et la bouche, ou un masque complet à adduction d'air (ventilation assistée) qui est indispensable pour les tâches particulièrement exposées, dans les conditions de travail exceptionnellement difficiles dans les cabines.
- S'il y a possibilité de contact avec la main lors des transvasements par exemple, il s'avère indispensable de porter des gants de protection adaptés à la tâche effectuée et au produit manipulé. Les gants en nitrile, néoprène, butyle sont les plus utilisés lors de la manipulation des solvants, des acides et autres produits utilisés dans le traitement des surface.
- Des bottes et vêtements (avec des protèges-bras, jambières et tablier long) résistants aux produits alcalins ou acides selon l'exposition.
- Des lunettes, écran faciaux de protection -
Une gestion des rejets et des déchets réglementaire
Les rejets atmosphériques de vapeurs de solvants sont fortement limités et réglementés dans le cadre de la directive européenne concernant les composés organiques volatils (directive COV 1999/13/CE) et une station de traitement des effluents est nécessaire pour répondre aux exigences environnementales.
Les bains et boues de traitement de surface ne doivent pas être rejetés dans le milieu naturel. Ils doivent :
- Soit être régénérés (techniques électrolytiques à compartiments séparés...),
- Soit être traités sur place dans des stations spécifiques ou, pour les faibles débits, sur des résines échangeuses d'ions,
- Soit être détruits par incinération dans des centres de traitement spécialisés, précipitation d'hydroxydes métalliques insolubles et déshydratation des boues minérales, récupération d'énergie... Les boues non valorisables doivent être stockées en centre de stockage de déchets ultimes (CSDU) de classe I.
Les boues de solvants, dans l'attente de leur traitement, doivent être récupérées dans un récipient étanche, étiquetées et entreposées dans un local ventilé et enlevées régulièrement vers des installations habilitées à les traiter par des sociétés spécialisées. Les Bordereaux de Suivi des Déchets Industriels (B.S.D.I.) attestent de la collecte des déchets par des entreprises autorisées, et de leur élimination conforme (à conserver pendant 5 ans en cas de contrôle). - La formation, par un organisme agréé, sur les dangers des produits utilisés et sur les moyens de se protéger, est indispensable : par exemple, comprendre les étiquettes du contenant des produits, connaître l'attitude à adopter en cas de fuite ou de déversement accidentel, savoir utiliser les E.P.I adéquats, formation incendie et premiers secours.
-
La surveillance médico-professionnelle
L'exposition aux produits de traitement de surface impose une surveillance périodique des travailleurs au moins une fois par an, instaurée par le médecin du travail, avec un suivi médical approprié (explorations fonctionnelles respiratoires et radiographies pulmonaires, recherche de symptômes respiratoires, de troubles neuropsychiques, réalisées en fonction de l'intensité et l'ancienneté de l'exposition).
Pour permettre une traçabilité des expositions, l'employeur doit établir la liste des salariés exposés aux produits dangereux et CMR (cancérogènes, mutagènes ou reprotoxiques), en précisant la nature de l'exposition, sa durée, son degré estimé par les contrôles effectués. (Article R. 4412-40 du Code du Travail).
Chaque salarié exposé à des produits chimiques dangereux doit faire l'objet d'une fiche d'exposition établie par l'employeur et bénéficier d'une surveillance médicale renforcée : le dossier médical comporte alors les dates et résultats des examens médicaux complémentaires pratiqués, le double de la fiche individuelle d'exposition et doit être conservé pendant au moins 50 ans après la fin de la période d'exposition. A sa sortie de l'entreprise, il doit recevoir une attestation d'exposition qui lui permettra de continuer à se faire suivre médicalement.
Pour aller plus loin
Dossiers INRS :
- Ateliers de traitement de surface. Prévention des risques chimiques. Santé et sécurité des personnes. ED 827, 1998.
- Ateliers de traitement de surface. Concevoir en sécurité intégrée. Création, extension, modification. ED 848, 2000.
- Solvants de dégraissage. Critères de choix et mesures de prévention. Fiche pratique de sécurité. ED 95, 2001
- Ateliers de traitement de surface. Guide d'identification des cuves, canalisations et équipements. ED 794, 2003.
- Cuves de traitement de surface. Guide pratique de ventilation n° 2. ED 651, 2007.
- Dégraissage des métaux. Choix des techniques et des produits. Fiche pratique de sécurité. INRS. ED 48, 2007.
Décembre 2011
Partagez et diffusez ce dossier
Laissez un commentaire
Votre adresse de messagerie ne sera pas publiée.