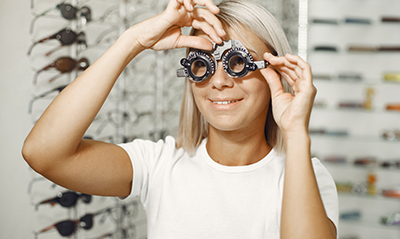
Les machines d'emballage et de conditionnement d'un grand niveau d'automatisation ont des rythmes élevés de fonctionnement qui sont susceptibles d'entrainer des risques importants de blessures, ce qui nécessite des systèmes de sécurité et des postes ergonomiques conçus pour minimiser ces dangers opératoires. Quant aux équipements semi-automatiques ou la chaine manuelle des opérations d'emballage et de conditionnement, ils exposent également les opérateurs aux gestes répétitifs et à la manipulation de charges et à tous les Troubles Musculo-Squelettiques (TMS) qui en découlent.
Les machines d'emballage et de conditionnement d'un grand niveau d'automatisation ont des rythmes élevés de fonctionnement qui sont susceptibles d'entrainer des risques importants de blessures aux travailleurs, ce qui nécessite des systèmes de sécurité et des postes ergonomiques conçus pour minimiser ces dangers opératoires.
Quant aux équipements semi-automatiques ou la chaine manuelle des opérations d'emballage et de conditionnement, ils exposent également les opérateurs aux gestes répétitifs et à la manipulation de charges et à tous les Troubles Musculo-Squelettiques (TMS) qui en découlent.
De plus, il y a des risques chimiques spécifiques aux différents produits emballés ou conditionnés : allergies aux contenants ou aux contenus, pollution de l'air ambiant suite à des fuites nocives de gaz propulseurs ou de composés organiques volatils ou des déversements de liquides toxiques ou corrosifs … dans le cas des marchandises dangereuses. Dans certains cas, en agro-alimentaire notamment, il y a des opérations de stérilisation au moyen de rayons UV ou Gamma exposant les opérateurs au risque radiologique.
Enfin, il faut prendre en compte les risques professionnels moins spécifiques à cette industrie, aux chutes de plain-pied, à la possibilité des contacts avec des conducteurs électriques sous tension, au bruit, à l' environnement froid, au travail en horaires décalés …
Ces risques des ateliers d'emballage et de conditionnement peuvent être maîtrisés par l'utilisation de machines et d'équipements conformes aux normes et de haute exigence ergonomique, par la présence d'une installation électrique et de protection incendie, une ventilation efficace, et par le respect des exigences essentielles de sécurité (lutte contre le bruit, hygiène des locaux…) et de protection individuelle, avec une attention soutenue pendant les périodes de mise en place des outillages et de démarrage de production, ou lors des opérations de maintenance et de réparation.
Les principaux risques professionnels dans l'industrie d'emballage et de conditionnement
Le conditionnement (ou packaging avec une connotation marketing) est le premier contenant ou enveloppe du produit, alors que l'emballage sert à la protection du produit pour le stockage, la manutention et le transport jusqu'au consommateur final. L'emballage et le conditionnement concerne toutes les industries manufacturières, produits agroalimentaires, électroménagers, chimiques, cosmétiques, pharmaceutiques, etc. pour le commerce de gros ou de détail. A la diversité considérable des produits à conditionner, en poudre, en pate, solides, liquides, gazeux, s'ajoute la très grande variété (forme, matière, taille ou quantité) des conditionnements et emballages en plastique (sacs, sachets), en verre (bouteilles, flacons), en papier carton, en métal (boîtes) ou en bois (palettes, tonneaux). Cela génère une extrême diversité de machines d'emballage et de conditionnement à usage industriel et commercial et des exigences de productivité et de sécurité aussi variées que les produits et leurs conditionnements : peseuses, doseuses, vibreurs anti-tassement, ensacheuses, housseuses, banderoleuses, étuyeuses, encartonneuses, fardeleuses, encaisseuses, remplisseuses, boucheuses, visseuses, filmeuses, thermoformeuses et operculeuses, lignes d'embouteillage … pour de petites, moyennes ou grandes séries.
Les machines de conditionnement accomplissent souvent des cycles de fonctionnement très rapides sur des produits parfois dangereux et des matériaux d'enveloppe délicats : de ce fait, les pannes de machines ont des conséquences très dommageables en terme économique (bris, entassement, déversement …) et sécuritaire (toxicité respiratoire ou cutanée). En général, les machines d'emballage et conditionnement sont intégrées au sein d'une transitique adaptée aux produits, avec des postes de travail robotisés ou des lignes automatisées ou des chaines d'emballage manuel. Dans les entreprises spécialisées, les ateliers de conditionnement fonctionnent en continu : les opérateurs sur machines automatisées de conditionnement sont donc amenés à avoir des horaires décalés et des horaires de nuit. Le travail peut s'effectuer dans le froid pour le conditionnement de certains produits comme la viande, par exemple. Enfin, la stérilisation par rayons ultraviolets ou par rayonnements ionisants, expose les conditionneurs à des risques radiologiques bien spécifiques pour des applications particulières, dans l'industrie agro-alimentaire notamment.
- Les risques physiques dans les ateliers d'emballage et de conditionnement
- Les risques mécaniques des machines
Certaines parties des machines en rotation ou en déplacement linéaire, les opérations de nettoyage et de maintenance, les réglages, les démarrages, sont sources d'accidents majeurs du fait des pièces en mouvement en particulier lors des mises en marche intempestives, des arrêts anormaux suite à un dysfonctionnement ou à une rupture d'énergie : coupures aux mains, lacérations des avant-bras ou écrasements lors des nettoyages par exemple, ou lors des déplacements des éléments mobiles des machines ou convoyeurs, cisaillement, entraînement, happement, friction, enroulement des cheveux et des vêtements par des rouleaux ou cylindres ou goulottes en rotation, fouettement de câble en cas de rupture …
Par ailleurs, de nombreux troubles musculo-squelettiques sont dus aux vibrations et aux mouvements répétés chez des travailleurs exerçant sur des machines qui fonctionnent à vitesse élevée : effets pathologiques sur le membre supérieur (tendinites, syndrome carpien), et sur la colonne vertébrale par transmission des vibrations au corps entier. Les risques de neuropathies par transmission des vibrations au bras se manifestent par la perte de dextérité manuelle, la diminution tactile des doigts, des fourmillements dans les mains intermittentes ou persistantes.
- Les risques physiques des manutentions manuelles
Les tâches de l'emballeur ou du conditionneur manuel sont effectuées debout ou assis. La manipulation des produits et des outils demande plus ou moins d'efforts physiques. Les risques attachés à l'exercice de l'activité (écrasement de doigts, coupures...) dépendent des outils utilisés. L'activité nécessite une attention constante et une habileté manuelle, avec un rythme de travail soutenu et des cycles courts d'opérations.
Ces travaux manuels dans les petits ateliers d'emballage (remplissage des cartons, étiquetage) et d'expédition (mise sur palette) exigent une gestuelle répétitive et rapide constitutive de risques de troubles musculo-squelettiques fréquents : par exemple, les opérations sur le tapis roulant et de mise en carton, impliquent de très nombreux gestes avec posture penchée, rotation du corps et déplacement qui augmentent la pénibilité du travail. Les accidents de manutention lors du port manuel de charges ou du fait d'un nombre excessif de manipulations ou de la station debout prolongée, entrainent un vieillissement progressif des structures ostéoarticulaires qui peut aboutir à une inaptitude professionnelle, ce qui, de par leur fréquence et leur impact, tant médical que socioprofessionnel, constitue un problème majeur de santé au travail pour les emballeurs et les conditionneurs.
Les emballeurs et conditionneurs figurent ainsi parmi les métiers les plus concernés par les troubles musculo-squelettiques (TMS), affections péri-articulaires provoquant des douleurs des poignets (syndrome du canal carpien), des coudes (épicondylite, épitrochléite), des épaules (tendinites des bras tendus) et des lésions chroniques de la colonne vertébrale de la position penchée et/ou en torsion (cervicalgies, lombalgies, et autres atteintes du rachis).
- Les risques sonores
Les sources de bruits dans les ateliers d'emballage et de conditionnement sont nombreuses : les niveaux de pression acoustique engendrés par les bruits des machines (sans insonorisation adaptée) dans les ateliers d'emballage et de conditionnement peuvent couramment atteindre 85 dB.
En dehors des atteintes au système auditif (déficit auditif, acouphènes…), le bruit ambiant peut entraîner une gêne ou un stress vecteur de troubles du psychisme et de pathologies qui nuisent non seulement à la santé du travailleur mais aussi à la sécurité de son travail par baisse de vigilance et de dextérité ou de concentration.
- Les risques liés au froid
Les personnes travaillant en ambiances froides, indispensables à la conservation de certains produits alimentaires (viande, poisson) subissent une exposition au froid qui peut s'avérer parfois importante.
Non seulement travailler dans un environnement froid peut être dangereux directement pour la santé, mais aussi indirectement du fait des risques liés à la baisse de dextérité manuelle et de vigilance mentale qui augmentent les taux d'accidents du travail.
Les engelures sont des lésions cutanées associées à l'exposition au froid, à la glace et à l'eau à basse température. Les doigts deviennent rouge violacés, douloureux, avec des crevasses et/ou des phlyctènes. L'exposition au froid est aussi susceptible de déclencher le syndrome de Raynaud (doigts blancs et douloureux par vasoconstriction).
Les ambiances froides associées à des courants d'air et à l'humidité de l'air favorisent aussi l'apparition d'affections aiguës des voies respiratoires supérieures.
- Autres risques physiques
D'autres risques physiques ne sont pas spécifiques aux ateliers d'emballage et de conditionnement, mais communs à toute activité industrielle : chutes de plain pied sur sol glissant, inégal ou encombré électrisation/électrocution par utilisation d'outillage défectueux … - Les risques chimiques dans les ateliers d'emballage et de conditionnement
Les dégagements nocifs gazeux ou pulvérulents peuvent être engendrés par le conditionnement en aérosol, par création d'atmosphère spéciale de protection, de désoxygénation ou de désaération (oxyde d'éthylène, argon, azote …), par les fuites ou déversements accidentels des produits conditionnés émanant des vapeurs ou poussières toxiques, notamment pour les composés organiques volatils (COV) des peintures, vernis, colles, décapants, solvants, résines, produits d'entretien ou phytosanitaires …
Les composés organiques volatils (COV) sont des substances qui se caractérisent par leur grande volatilité, c'est-à-dire qu'ils émettent des vapeurs même à pression et température ordinaire de travail, et donc se répandent aisément sous forme gazeuse dans l'air ambiant des ateliers.
Les composés organiques volatils ont des effets très néfastes sur la santé (irritations des yeux, des muqueuses des voies respiratoires, troubles cardiaques et du système nerveux, céphalées, nausées…) et certains COV sont cancérigènes, d'autres toxiques pour la reproduction ou mutagènes. De plus, au contact d'une source de chaleur, beaucoup de COV présentent des risques importants d'incendie et d'explosion.
La stérilisation par l'oxyde d'éthylène, utilisée pour les produits médicaux et pharmaceutiques, s'obtient par infiltration du gaz dans l'emballage : ce gaz forme un mélange explosif avec l'air ambiant et est très toxique : céphalées pouvant mener à des convulsions, irritant pour la peau et les poumons, classé cancérogène et mutagène. La rupture accidentelle du conditionnement due à procédures de travail inadéquates ou à un dysfonctionnement d'une machine peuvent entraîner la possibilité de contact cutané avec des substances liquides corrosives (acides, caustiques …) ou allergisantes, par exemple dans le cas des détergents, désinfectants …. : brûlures cutanées ou oculaires dans le cas de projections, ou sensibilisations allergiques (eczéma, asthme…).
Les produits de dégradation de film plastique scellé à chaud peuvent être responsables d'asthme. - Les risques radiologiques dans les ateliers d'emballage et de conditionnement
La capacité de tuer les cellules vivantes des rayons ultra-violets et Gamma permet l'application de cette propriété à la stérilisation pour la conservation des aliments ou des produits cosmétiques et pharmaceutiques, en éliminant les bactéries avec des lampes UV germicides ou des sources radioactives (cobalt 60).
L'industrie utilise des rayons UV artificiels de différentes longueurs d'onde et intensités, à des niveaux souvent plus élevés que le rayonnement solaire et avec des longueurs d'ondes plus nocives (UVC), ce qui rend le rayonnement UV artificiel intrinsèquement beaucoup plus dangereux pour la santé : l'exposition professionnelle intense et/ou prolongée aux rayons UV génère des risques cutanés (brûlures, cancers …) et oculaires (conjonctivites, cataractes…).
Le pouvoir de pénétration profonde et d'ionisation de la matière confère aux rayons Gamma la capacité de créer d'importants dommages corporels : atteintes cutanées, ophtalmologiques, hématologiques, cellulaires pouvant provoquer des cancers, des malformations fœtales.
Les mesures préventives des risques professionnels en emballage et conditionnement
Les opérations sont aujourd'hui pour une large part automatisées et mécanisées avec des machines spéciales d'emballage et conditionnement. Le process des grandes entreprises ainsi fortement modernisé permet de réduire l'exposition des travailleurs et de diminuer considérablement les risques physiques et chimiques. Le process d'une installation piloté par un contrôle informatisé centralisé réduit les interventions dans les ateliers et minore ainsi beaucoup les possibilités de sources d'exposition chimique et physique. Toutefois, des incidents dans l'automatisation des opérations, des fuites, des dysfonctionnements des asservissements… génèrent des dangers et nécessitent également des interventions de maintenance qui restent dangereuses. Par ailleurs, dans les petites entreprises dans lesquelles les volumes traités sont bien inférieurs, les pratiques sécuritaires sont beaucoup moins mises en œuvre et maîtrisées. La prévention la plus efficace est la prévention primaire avec la mise en place de technologies qui permettent des actions sur les produits (suppression ou emploi de produits de substitution de moindre impact potentiel sur l'homme) et/ou des actions sur les procédés (emploi de matériels ou de machines supprimant ou limitant au maximum les impacts, par de bas niveaux sonores…).
Toutes les machines doivent être conçues pour minimiser le risque opératoire (barrière virtuelle ou matérielle) et le risque sonore.
Les moyens de prévention à mettre en œuvre pour pallier les risques professionnels dans les ateliers d'emballage et conditionnement résident ensuite dans la prévention collective (ventilation efficace de l'atelier, installation électrique et de protection incendie conformes aux normes, respect des règles générales d'hygiène…) qui diminue fortement les expositions et la fréquence ces accidents, puis dans la prévention individuelle (équipements de protection) qui en diminue nettement la gravité, enfin dans la l'information et la formation à la sécurité des travailleurs.
Les ateliers des ateliers d'emballage et conditionnement doivent faire l'objet d'une analyse poussée des risques pour permettre la rédaction du Document Unique de Sécurité en appréciant à la fois l'environnement matériel et technique (outils, machines, produits utilisés) et l'efficacité des moyens de protection existants et de leur utilisation selon les postes de travail.
Les analyses de risques sont confiées à des spécialistes de la sécurité au travail (hygiéniste, ingénieur sécurité). Les rapports d'intervention et de maintenance seront aussi intégrés à la documentation de sécurité au travail de l'entreprise et communiquées au médecin du travail et au CHSCT.
- Dispositifs de sécurité des machines.
L'automatisation totale ou partielle des process avec des machines inadaptées augmentent les risques auxquels sont exposés les utilisateurs des installations ou les personnes situées à proximité. Des systèmes de sécurité performants doivent à la fois ne pas entraver le process de fabrication et assurer sans cesse et en toute circonstance l'intégrité physique des opérateurs.
Toute machine doit porter les avertissements, signalisations et dispositifs d'alerte indispensables pour assurer la sécurité des travailleurs afin de supprimer ou réduire au minimum les risques de coupure, d'entraînement, d'écrasement, de cisaillement causés par les éléments exerçant une action directe ou indirecte (transitique). Cette identification doit être réalisées par des pictogrammes et couleurs normalisées. Les éléments de travail doivent être disposés, protégés, commandés ou équipés de façon telle que les opérateurs ne puissent atteindre la zone dangereuse, tout en permettant une très bonne accessibilité machine pour les réglages et l'entretien.
Les panneaux de signalisation seront choisis et disposés de façon à être perçus et compris facilement sans ambiguïté. Chaque machine doit être munie d'un ou plusieurs dispositifs d'arrêt d'urgence clairement identifiables, accessibles et en nombre suffisant, permettant d'éviter les situations dangereuses en train de se produire :
- Ecrans de protection et de sécurité des opérateurs : protecteurs fixés à l'aide de moyens imposant un outil pour leur démontage ou par des protecteurs mobiles associés à un dispositif de verrouillage.
- Interrupteurs de sécurité.
- Barrières immatérielles de sécurité : des dispositifs électrosensibles de détection de présence et /ou de mouvement verrouillent les mouvements des parties mobiles pendant la présence d'un opérateur.
- Capteurs pour mesurer les températures et réguler les dispositifs de chauffage et éviter les surchauffes productrices d'émanations de décomposition thermique dangereuses
- Capteurs pour mesurer les pressions et réguler les dispositifs mécaniques et thermiques et éviter les surpressions internes.
- Ces capteurs sont intégrés dans des systèmes de commande et de contrôle gérés par des automates programmables.
- L'éloignement du personnel des zones dangereuses se fait au moyen d'obstacles fixes tels que panneaux fixes, pleins ou grillagés.
- Pour le cas des sources artificielles de rayons UVC, la réglementation visant de telles sources limite l'intensité des rayons UVC mais il est également nécessaire d'installer des capots de protection ou des écrans spéciaux et des dispositifs de verrouillage pour prévenir toute exposition et de veiller à ce que le personnel ne contourne pas ces dispositifs de sécurité.
- Pour le cas des sources de rayonnement Gamma, mise en œuvre des mesures de radioprotection visant à empêcher ou à réduire les effets nocifs des rayonnements ionisants : éloignement maximal des travailleurs par rapport aux sources de rayons Gamma, avec l'utilisation d'appareils manipulables à distance, dans un local indépendant et protégé.
La vérification de la mise en place, du bon état de la fonctionnement des protecteurs, des dispositifs de verrouillage ou d'inter-verrouillage et dispositifs de protection (arrêt d'urgence…) est fondamentale, pour assurer par exemple les consignes d'arrêt obligatoire, notamment lors des incidents et des opérations de maintenance, pour lesquelles une véritable procédure de consignation et déconsignation doit être mise en œuvre : en particulier, le cadenassage fait appel à des dispositifs d'isolation tels que les coupe-circuit, les cadenas et systèmes de cadenassage à distance, notamment pour la neutralisation des sources d'énergie avant tout travail d'entretien ou de réglage.
Le respect des recommandations des constructeurs et un entretien régulier des machines sont des éléments essentiels pour limiter les risques accidentels et pour prévenir des émanations. Ainsi l'utilisation et l'entretien des machines doivent être effectués par un personnel qualifié, spécifiquement formé (respect scrupuleux des capacités nominale des machines…) : de nombreux cas de fuites accidentelles peuvent survenir au niveau de différents équipements, ce qui entraîne la nécessité d'une maintenance rigoureuse des machines avec contrôle de l'étanchéité.
Des machines utilisées de manière non conforme ou mal entretenues et non vérifiées périodiquement créent un risque chimique supplémentaire. En particulier, les canalisations flexibles doivent être vérifiées périodiquement et remplacées en cas d'usure ou de choc, et en fonction de la durée maximale d'utilisation.
Les équipements à rayons Gamma doivent être contrôlés régulièrement (lors des contrôles règlementaires périodiques par un organisme agréé, du contrôle qualité des installations, …), notamment pour vérifier le bon réglage des appareils. Le contrôle doit être systématique pour les appareils générateurs de rayons Gamma lors de l'installation et chaque fois qu'ils ont subi une transformation, tous les ans pour les appareils mobiles, tous les 3 ans pour les appareils fixes.
En effet, un rayonnement parasite peut provenir de pièces défectueuses, d'un mauvais ajustement des accessoires à l'origine de fuites par des ouvertures non blindées et il convient de vérifier le bon fonctionnement de tous les blindages. On doit tenir un cahier de suivi de l'étalonnage des appareils de contrôle de débit de dose et des résultats de mesure. - L'ergonomie et l'organisation du travail
Les opérations d'emballage sur un tapis roulant et de remplissage de cartons ou autres contenants (barquettes …), impliquent de très nombreux gestes rapides et répétitifs avec rotation du corps et déplacement latéral : l'ergonomie des installations est primordiale pour réduire la pénibilité du travail (par exemple, rapprocher le point de préhension pour éviter une posture penchée) et prévenir l'apparition de troubles musculo-squelettiques, ainsi que des accessoires tels les sièges « assis-debout » et tapis antifatigue. L'instauration d'un système de rotation des travailleurs permet de varier les gestes et postures.
Les nombreuses manutentions manuelles de charges qui entraînent des risques évidents de troubles musculo-squelettiques au niveau du dos et des articulations, peuvent être aussi réduits par l'utilisation systématique de manutention assistée et de moyens de mise à niveau et de préhension des charges : diables, chariots, moyens de levage appropriés… - Une ventilation des lieux de travail adéquate
Les risques chimiques que peuvent présenter les dysfonctionnements des opérations de conditionnement et les fuites et ruptures d'emballage de produits dangereux confère à la ventilation et à l'aération des lieux de travail un rôle essentiel pour limiter la concentration de l'ensemble des gaz, poussières et vapeurs toxiques dans l'air ambiant et les évacuer des lieux de travail, de façon à éviter ainsi les conséquences sur la santé des travailleurs. Une ventilation et un appoint d'air appropriés sont aussi indispensables pour empêcher l'accumulation de mélanges inflammables dans l'air.
La ventilation mécanique générale doit assurer un renouvellement d'air en permanence afin de limiter les risques pour la santé, en évitant l'accumulation de vapeurs nocives et explosives, par extraction et soufflage : l'air est transporté dans le local par un ventilateur de soufflage et extrait du local par un ventilateur d'évacuation. L'extraction de l'air se fait grâce à un système de collecte par ces ventilateurs, des gaines de diffusion, et un réseau de conduits qui captent et concentrent les poussières et vapeurs jusqu'aux filtres et aux épurateurs qui permettent de nettoyer l'air, puis de l'évacuer à l'extérieur par rejet dans l'atmosphère.
Les composants aérauliques comme les ventilateurs, les conduits entre autres doivent être accessibles et faciles d'entretien et de nettoyage. En particulier, les réseaux s'encrassent rapidement avec de filtres hors d'usage, une évacuation des condensats obstruée… : une surveillance régulière de l'atmosphère est nécessaire pour vérifier l'efficacité des mesures d'aspiration par dosages atmosphériques. - Une installation électrique conforme
L'incendie et/ou l'explosion peuvent provenir des équipements électriques, et en particulier, l'équipotentialité et la bonne mise à la terre de toutes les installations métalliques doivent être contrôlées, les prises défectueuses remplacées, il faut éviter toute accumulation d'électricité statique ….
Les étincelles, arcs et échauffements provoqués par les moteurs et appareillages électriques en fonctionnement peuvent aussi déclencher la catastrophe.
Il convient d'utiliser de l'appareillage électrique conçu pour atmosphères dangereuses afin de prévenir que le matériel, y compris l'éclairage, soit à l'origine d'un incendie ou d'une explosion.
Une métallisation au moyen d'un matériel conducteur et une mise à la terre appropriées de l'équipement de traitement et de manutention sont utiles pour dissiper et diriger à la terre en toute sécurité les charges électriques accumulées. La protection contre les contacts avec les masses mises accidentellement sous tension est obtenue par un dispositif de coupure automatique en cas de défaut d'isolement.
Dans le domaine des atmosphères explosives (Atex), des normes européennes fixent le cadre de travail des industriels et des installateurs. Tout site de type Atex doit être équipé avec du matériel certifié, avec des enveloppes antidéflagrantes : c'est notamment obligatoire lors des procédés d'injection d'oxyde d'éthylène dans les emballages, ou les zones concernées doivent être mise sous alarme, à l'aide de détecteurs de gaz installés en différents lieux, pour surveiller toute présence de fuite. - La lutte contre le bruit
Les machines et équipements doivent être conçues et fabriquées de façon à ce que les émissions sonores soient réduites au niveau le plus bas possible en application d'une directive européenne 2003/10/CE du 6 février 2003 concernant les prescriptions minimales de sécurité et de santé relatives à l'exposition des travailleurs aux risques dus aux agents physiques liés au bruit.
Par le choix ou l'achat de machines et par l'utilisation de procédés silencieux, les émissions sonores peuvent être maintenues à un bas niveau.
Les machines bruyantes seront, selon les possibilités, munis de capots insonorisants et pour réduire les bruits transmis par les sols et les structures, des blocs anti-vibrations peuvent être placés entre la machine et la surface d'appui.
Les échappements d'air comprimé des circuits pneumatiques sont à équiper d'un silencieux.
Les postes de commande et de contrôle peuvent se situer dans un local séparé avec une isolation phonique. En ce qui concerne les locaux, les réflexions sur les murs entraînent une augmentation du niveau sonore dans le local et des mesures préventives de correction acoustique comme la mise en place d'un plafond absorbant, de cloisons amovibles à proximité des installations, réduisent à la fois le niveau sonore et protègent les postes de travail avoisinants. - Une bonne hygiène et entretien des locaux
Une bonne tenue des locaux et des sols est essentielle pour éviter l'accumulation de déversements et de poussières sous ou autour des machines. Les déversements peuvent créer un danger de glissement et par conséquent doivent être nettoyés immédiatement.
Les glissades, les pertes d'équilibre sont souvent provoquées par un sol défectueux ou un trébuchement contre un obstacle non repéré. Il faut donc veiller à maintenir l'ordre dans tous les locaux : les voies de circulation doivent être débarrassées de tout obstacle, des revêtements de sol antidérapants doivent être privilégiés, les inégalités de surfaces et/ou obstacles doivent être soit supprimés soit clairement signalés, notamment dans les lieux de passage. Des postes de rinçage oculaire et les douches de sécurité doivent se trouver à proximité des postes de travail. - Le port d'équipements de protection individuel adéquat
Les équipements de protection individuelle sont nécessaires pour réduire le risque d'exposition non totalement éliminé par les mesures de protection collectives précédentes : selon les cas, casque, gants, vêtements de protection, chaussures et lunettes de sécurité (avec filtres pour l'ultraviolet si nécessaire), tenue adaptée si travail au froid, protections auditives.
En cas d'urgence ou pour des travaux exceptionnels d'entretien de courte durée, si le système de ventilation ne suffit pas à empêcher l'accumulation de vapeurs ou de poussières, des masques respiratoires filtrants doivent être fournis.
Dans l'agroalimentaire, de manière à ce que le personnel ne soit pas en contact avec le produit, une tenue est obligatoire, car elle évite la contamination qui pourrait venir des habits de ville. La tenue doit couvrir le corps et les bras (blouse, combinaison, tablier imperméable …), la charlotte la tête. - La formation et l'information du personnel
La formation, par un organisme agréé, sur les dangers des produits utilisés et sur les moyens de se protéger, est indispensable : par exemple, comprendre les étiquettes du contenant des produits, connaître l'attitude à adopter en cas de fuite ou de déversement accidentel, savoir utiliser les E.P.I adéquats, formation aux premiers secours et incendie… La formation aux bons gestes et postures en manutentions manuelles est au cœur du dispositif de prévention de l'emballeur et du conditionneur : la mise en place de formations PRAP (Prévention des Risques liées aux Activités Physiques) est un des moyens permettant de lutter contre tous les troubles musculo-squelettiques dus à des positions articulaires inadéquates, en appliquant les principes de base de sécurité physique et d'économie d'effort.
Novembre 2015
Partagez et diffusez ce dossier
Laissez un commentaire
Votre adresse de messagerie ne sera pas publiée.