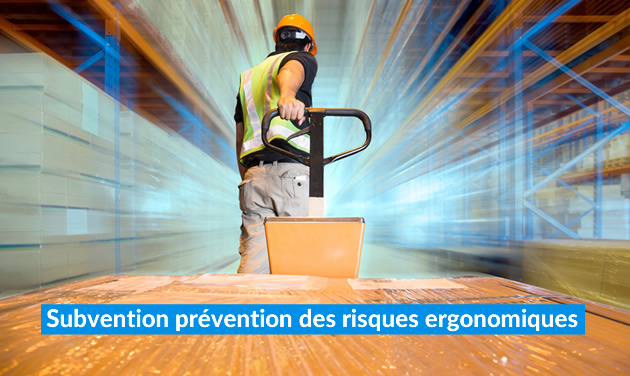
La prévention des risques professionnels de l’industrie 4.0
Quatrième révolution industrielle, l’industrie 4.0 est celle de la numérisation complète de moyens de production automatisés, connectés et communicants entre eux, pouvant être pilotés en temps réel et à distance et incorporant de l’intelligence artificielle, avec usage de la réalité virtuelle et de la réalité augmentée.
Après la mécanisation, la massification et l'automatisation de la production des trois phases historiques précédentes de l’industrialisation des XIXème et XXème siècles, l’industrie numérisée et connectée du XXIème vise à la fois une meilleure productivité, qualité, flexibilité, traçabilité, sécurité des opérations de fabrication :
- lignes de production et logistique performantes, sûres, ergonomiques, mises au point et optimisées grâce à la simulation virtuelle, fiabilisées par une maintenance prédictive gérée par l’Intelligence Artificielle et un entretien préventif amélioré avec la réalité augmentée ;
- modes de production, de distribution et d’administration flexibles et communicants et outils de production (fabrication additive par impression 3D, objets connectés ...) reconfigurables et capables de fournir des produits et services individualisés ;
- chaines de montage robotisées, robots collaboratifs (cobots), exosquelettes délivrant les travailleurs des tâches pénibles et/ou répétitives, démultipliant la rapidité et l’efficacité opératoires et évitant l’exposition à des ambiances de travail dangereuses.
L’organisation du travail est totalement modifiée par ces transformations de l’ensemble des composantes du process de fabrication (opérateurs, produits et machines) : en particulier, les opérateurs doivent évoluer vers des tâches à plus forte valeur ajoutée. Ainsi, de gros efforts de formation, d’adaptation des travailleurs sont nécessaires face à ces modifications technologiques et organisationnelles profondes et rapides et des mesures doivent être mises en œuvre pour que la prévention des risques professionnels soit prise en compte dans ce nouveau contexte de tâches, métiers, procédures et compétences.
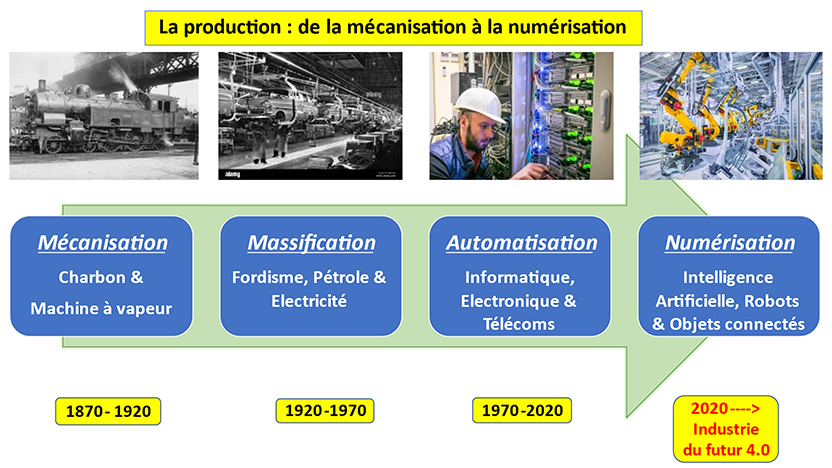
Les niveaux et étapes de déploiement de l’industrie 4.0
L’industrie 4.0 s’appuie sur une le déploiement des Technologies de l’Information et de la Communication (TIC) au sein des processus de production et de logistique de l’entreprise et sur la combinaison de technologies de production de pointe : les robots collaboratifs, les robots mobiles, les exosquelettes, l’impression 3D (ou fabrication additive) ainsi que l’intelligence artificielle, la réalité virtuelle et la réalité augmentée ...
La transformation digitale des usines et l’interconnexion numérique de l’ensemble des composantes du process de fabrication est un élément clé de l’industrie 4.0, ce que permet l’essor des systèmes de traitement de l’information, de l’Internet des Objets (IoT), du Big Data, du Cloud Computing ou encore de l’Intelligence Artificielle (IA) et du Machine Learning.
L’opérateur 4.0 utilise ces technologies qui visent à « augmenter » les capacités de l’homme, notamment ses capacités physiques (via l’utilisation d’un exosquelette ou d’un robot collaboratif par exemple) et ses capacités sensorielles (via le recours à la réalité augmentée par exemple et façon plus large aux objets connectés).
Différents niveaux d’implémentation de l’ industrie 4.0 avec une logique incrémentale d’interconnexion et d’Intelligence Artificielle doivent être considérés :
Première étape : La connectivité est l’enjeu primordial : il est essentiel de faire communiquer les machines avec le réseau d’entreprise, de façon sécurisée. Les TIC connectent l’ensemble des nouvelles technologies de l’usine et permettent d’établir une communication continue d’informations relatives aux processus de production et aux produits.
Deuxième étape : Implantation de l’Intelligence Artificielle au moyen du Machine Learning et de la connexion au Big Data et au Cloud Computing. Alimentés par l'intelligence artificielle (IA), les systèmes de production vont au-delà de l'automatisation basique. Il devient alors aussi possible de prédire les événements à venir (par exemple, quand une machine aura besoin de maintenance) pour permettre de prendre des décisions éclairées. Les technologies d'assistance procurent aux collaborateurs des suggestions, des conseils et des recommandations pour faire évoluer les process.
Troisième étape : Intégration de l'autonomie aux systèmes de contrôle industriels qui s'adaptent en temps réel à l'évolution des environnements dynamiques et/ou des entrées variables avec des processus flexibles. Il est possible alors de réaliser des autodiagnostics, des autocontrôles et de permettre l’autoadaptation des procédés et des équipements de production sans intervention humaine.
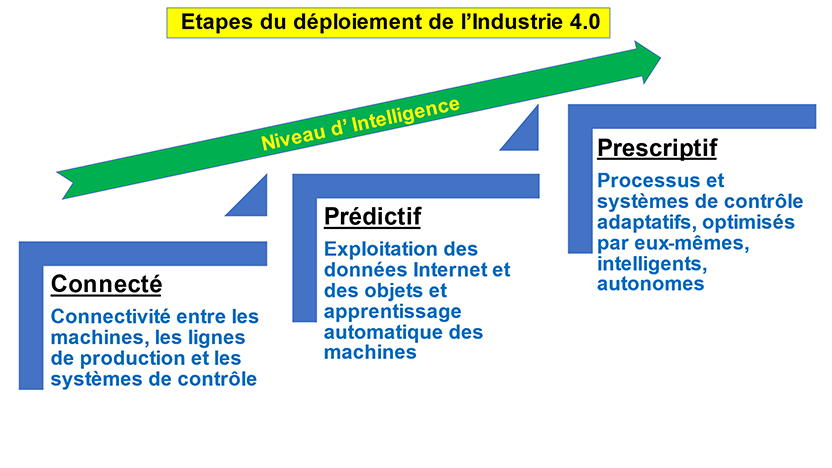
Les briques technologiques de l’industrie 4.0
La qualité et le rendement dans l’industrie 4.0 augmentent considérablement avec des opérations de fabrication intelligentes, sécurisées et adaptables, grâce à l’utilisation concomitante de plusieurs technologies :
- L’intelligence artificielle
L’intelligence artificielle s’inspire de l’intelligence naturelle avec des systèmes ou des machines qui imitent l’intelligence humaine pour effectuer des tâches complexes à partir d’algorithmes et d’informations collectées provenant de sources multiples dans l’environnement, tout en s’améliorant grâce à l’apprentissage et à l’expérience.
Les applications dotées d’intelligence Artificielle (IA) sont pilotées par un logiciel qui se caractérise par sa capacité à analyser de grands volumes de données (Big Data), et par des algorithmes qui le rendent capable d’apprentissage (Machine Learning), leur conférant une certaine autonomie ; en particulier avec l’apprentissage profond (Deep Learning) qui consiste à ce que l’IA acquière de nouvelles compétences à travers un réseau neuronal en couches multiples.
Les méthodes et outils numériques du Big data sont utilisés pour la capture, la recherche, le stockage, le partage et le traitement rapide de grandes quantités de données non structurées et hétérogènes.
Le Cloud computing consiste à utiliser la puissance de calcul ou de stockage de serveurs informatiques distants à travers le réseau Internet. - La robotique
Le robot industriel est une structure mécanique dotée d'un bras manipulateur programmable généralement avec six degrés de liberté, trois axes destinés au positionnement et trois axes pour l'orientation, permettant de déplacer et manipuler un outil effecteur dans un espace de travail donné et contrôlé par des capteurs divers. Certains robots utilisent comme énergie de fonctionnement des moteurs électriques, d'autres utilisent aussi des vérins hydrauliques.
La programmation des mouvements et des séquences d'un robot industriel sont réalisées au moyen d'un microordinateur industriel ou automate programmable doté du logiciel adéquat.
Les robots industriels sont le plus souvent affectés à des opérations spécifiques (soudure, peinture, découpe, assemblage, manutention, conditionnement ...) en exécutant des consignes assez simples à un poste fixe, mais, grâce aux progrès de l'intelligence artificielle, des capteurs et de la mécatronique, on voit apparaître de plus en plus des robots dotés d'une vision et de possibilités d'apprentissage, de mobilité et d'autonomie. Le robot mobile est doté de plus de moyens de locomotion qui lui permettent de se déplacer sous son propre contrôle. - La cobotique
Les robots collaboratifs (cobots) aux postes de travail les plus dangereux ou les plus pénibles (service professionnel, assistance physique ...) interagissent avec les opérateurs qui partagent un même espace de travail, en réalisant des travaux avec eux. Les utilisations nouvelles des robots industriels collaboratifs, comme l'aide ou l'assistance à la manipulation de charge, permettent de les sortir des usines et de travailler sur les chantiers du BTP par exemple. L'offre robotique développée par les progrès de l'intelligence artificielle (capacité et rapidité de calcul et apprentissage), de la communication, et de la mobilité mécatronique, sort ainsi les robots de leur cage et les fait évoluer à proximité de leur utilisateur. - Les objets connectés et Internet des objets (IoT)
Les objets connectés sont capables de collecter, voire d’analyser des données et de les échanger entre eux ou avec des bases de données. Les objets connectés captent, stockent, traitent, transmettent des données, et peuvent communiquer avec d'autres systèmes pour obtenir ou fournir de l'information, avec la capacité à se connecter à un réseau d'information plus large, appelé Internet des Objets ou Internet of Things (IoT).
On distingue les objets connectés portables (wearables) comme les lunettes, bracelets, casques, vêtements, trackers d'activités (contrôle d'accès, suivi opérationnel...) et les objets connectés intégrés dans un processus pour des applications industrielles (sécurité et gestion technique des bâtiments, chaîne logistique, maintenance préventive des machines ...).
L’internet des objets (IoT) connecte les opérateurs, les processus, les données et les objets (équipements, machines, appareils, outils ...) déjà connectés entre eux, à un réseau plus large au travers d’un même réseau informatique, avec des informations en temps réel. - Les exosquelettes
Les exosquelettes de travail sont des structures articulées externes d’assistance à l’effort, portées par l’opérateur, mécaniques, électromécaniques ou mécatroniques, destinées à renforcer les capacités physiques des travailleurs, notamment pour soulager le port manuel de charge, les postures contraignantes et les gestes répétitifs. Ces nouvelles solutions exo-squelettiques au travail, motorisées (combinaison robotique) ou non, vont se propager rapidement dans de nombreux secteurs, ceux de la logistique ou de la préparation de commandes, des chantiers du BTP, des usines manufacturières (automobile, ...), de l’agriculture et des soins infirmiers etc. - La fabrication additive ou impression 3D
L’impression tridimensionnelle (3D) d’une pièce est la fabrication additive par couches successives de matériaux de base (thermoplastiques liquéfiés, photopolymères, poudres métalliques, etc.) par des procédés pilotés par un logiciel. L’impression tridimensionnelle s’appuie sur plusieurs types de technologies, mais basées toutes sur la découpe numérique d’un objet virtuel 3D en lamelles 2D de très fine épaisseur, ensuite déposées physiquement une à une par l’imprimante en les fixant sur les précédentes, pour obtenir l'objet réel étape par étape : la production additive, par couches successives, génère de petites quantités de matériaux jusqu’à l’obtention d’un produit en trois dimensions, numérisé en couches dans un fichier CAO (Conception Assistée par Ordinateur). L’utilisation des imprimantes 3D dans les « fab labs » (ou « ateliers de fabrication numérique ») est en forte croissance dans de nombreux secteurs. - La Réalité Virtuelle et la Réalité Augmentée
Les réalités virtuelle (RV, VR en anglais) et augmentée (RA, AR en anglais) ont ouvert de nouvelles perspectives, notamment pour la simulation des situations de travail et des risques, la formation (immersive learning et immersive training), la maintenance des équipements, l’assistance au suivi de procédures et pour l’ergonomie des postes de travail (ergo-conception). L’intérêt, l’efficacité et l’acceptabilité de ces techniques prennent de plus en plus d’importance, à mesure des améliorations considérables offertes par les moyens informatiques, les objets connectés et les logiciels des « jeux sérieux » (serious games).
Avec un essor considérable, la RV et la RA sont de plus en plus utilisées dans les secteurs industriels et dans les services, en utilisant trois principes : immersion, navigation et interaction.
À la différence de la réalité augmentée (qui complète le réel par des éléments virtuels), la réalité virtuelle crée une situation entièrement virtuelle construite par ordinateur. La réalité virtuelle permet à l’utilisateur de s’immerger ou d’interagir en temps réel avec une maquette numérique d'un procédé, d'un poste de travail, d’un atelier ou d'une usine. - Cybersécurité
Les réalités virtuelle (RV, VR en anglais) et augmentée (RA, AR en anglais) ont ouvert de nouvelles perspectives, notamment pour la simulation des situations de travail et des risques, la formation (immersive learning et immersive training), la maintenance des équipements, l’assistance au suivi de procédures et pour l’ergonomie des postes de travail (ergo-conception). L’intérêt, l’efficacité et l’acceptabilité de ces techniques prennent de plus en plus d’importance, à mesure des améliorations considérables offertes par les moyens informatiques, les objets connectés et les logiciels des « jeux sérieux » (serious games).
L'usine 4.0 étant totalement connectée, les risques de pénétration et d'attaques sur des systèmes de contrôle informatiques et industriels deviennent majeurs. La cybersécurité est donc une problématique clé, qui doit être intégrée à toute nouvelle implémentation, pour ne pas ouvrir la porte à de nouvelles menaces.
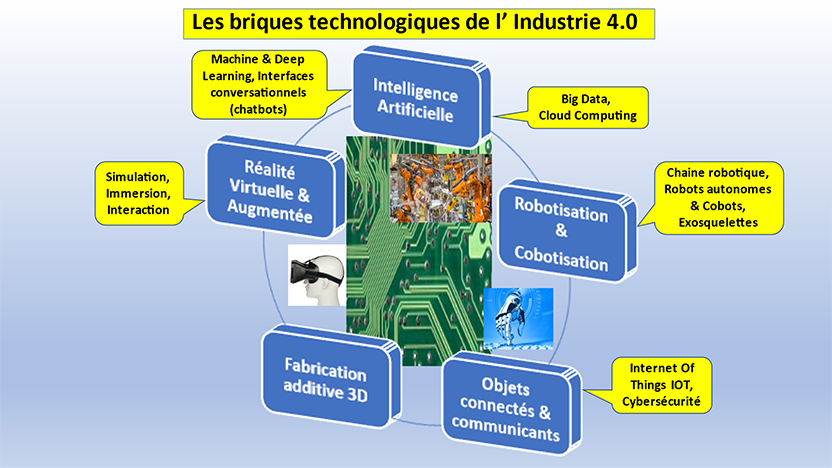
Les mesures de prévention des risques professionnels de l’Industrie 4.0
La mise en œuvre de l’industrie 4.0 et la numérisation de l’ensemble des activités industrielles modifient la fonction du travailleur et ses relations interpersonnelles dans l’entreprise. En matière de santé et sécurité au travail (SST), la numérisation des activités et des relations génère de nouveaux risques comme une charge mentale en augmentation et un décloisonnement des sphères privées et professionnelles. Dans l’industrie 4.0, l’automatisation et la digitalisation transforment certaines usines en quasi-lieux de science-fiction supervisés par un minimum d’humains ou par le développement du travail collaboratif entre robots et humains.
En ce qui concerne la prévention des risques professionnels, une vigilance particulière, voire un encadrement éthique, sont donc nécessaires à propos de l’utilisation des technologies de l’industrie 4.0 : il y a intérêt d’accompagner le changement lié à un projet de développement de l’industrie 4.0 par une démarche globale et participative au niveau de l'entreprise. C’est ainsi que l’entreprise pourra conjurer les menaces de ces innovations et profiter des opportunités que recèlent toujours une situation évolutive ou une période de transition et d’incertitude, en facilitant l'acceptation des changements et en réduisant les facteurs de rejet, notamment chez les travailleurs les plus âgés.
Les facteurs déclencheurs de changement créent souvent une véritable rupture, car il y a remise en cause de la manière d’agir des acteurs concernés : ils brouillent profondément les repères, et ces modifications touchent tous les niveaux de l’organisation du travail. D’où anxiété, sentiment de perte des repères, de savoir-faire ou de pouvoir : ces profonds changements dans les organisations industrielles ou tertiaires, avec des transformations importantes des postes et méthodes de travail, sont anxiogènes et sources de risques psychosociaux fréquents. La phase de formation et de familiarisation des utilisateurs est primordiale et il ne faut pas négliger le temps nécessaire à son acceptation sociale de ces évolutions technologiques et organisationnelles.
Le travailleur va être placé dans un nouveau contexte de l’industrie 4.0 ou la pénibilité de son travail et ses taches physiques sont réduites, en transformant son rôle d'opérateur à celui de pilote, en augmentant le recours à ses capacités cognitives, ce qui requiert des actions d’anticipation et d’accompagnement afin de favoriser sa formation et son adaptation aux évolutions technologiques et des procédés de fabrication. Car automatiser les tâches à faible valeur ajoutée, répétitives, pénibles, implique de recentrer l’opérateur sur des tâches à plus forte valeur ajoutée : redéfinition des procédures et des rôles, acquisition de nouveaux savoir-faire, nouvelles compétences à déployer. Les personnes travaillant dans de nombreux emplois existants devront voir leurs rôles évoluer et améliorer leurs propres capacités avec les technologies de l'IA : cette IA, utilisée d’abord pour automatiser des éléments répétitifs de leur travail quotidien, imposera aux travailleurs de se concentrer sur des domaines qui nécessitent plus de créativité, imagination, intelligence émotionnelle, avec les fortes contraintes d’adaptation que cela requiert et les possibles troubles psychosomatiques que cela engendre. Ces évolutions techniques majeures entrainent une remise en question des expertises notamment des seniors qui peuvent ainsi être mis dans des situations d'incompétence générant une forte déstabilisation personnelle : d'où de réelles difficultés à s'adapter aux nouvelles technologies ou procédures au travers de la formation, et le développement de sentiments de frustration et d'échec conduisant à une démotivation, le tout dans un cercle vicieux de désinsertion professionnelle.
Une bonne conduite du changement va consister à anticiper ces risques psychosociaux, définir et mettre en œuvre une démarche permettant la mise en place du projet sans perturbations majeures vers de nouveaux contextes de travail, de nouvelles tâches et responsabilités, de nouvelles compétences.
-
L’usage de l’intelligence artificielle en entreprise soulève des questions nouvelles relatives aux risques professionnels et à la protection des travailleurs des conséquences des transformations nombreuses du travail : si une application l’utilise, il faut par exemple s’assurer que les données ne soient pas biaisées de façon à ne pas donner de résultats discriminants en matière de gestion des Ressources Humaines notamment. Au-delà des risques physiques induits par le dysfonctionnement d’un robot, des risques psychologiques sont en particulier liés à l’interaction homme-machine : sentiments de dépendance, de perte d’autonomie et d’identité, excès de charge mentale ....
Les préoccupations croissantes des risques de l’intelligence artificielle et du Machine Learning en entreprise tient à son intégration dans les machines automatisées et dans le monitoring du travailleur, avec des enjeux juridiques, éthiques, sociaux et réglementaires : l’apparition du technostress, l’exploitation des données personnelles sur les lieux de travail, les dimensions de sécurité et de latitude décisionnelle des interactions entre l’être humain et la machine, la transparence des algorithmes de surveillance etc.
Si l’IA en entreprise recèle ainsi de nombreuses potentialités, elle engendre aussi des risques professionnels nouveaux plus difficiles à appréhender dont la gestion est complexe et encore incertaine : d’une part, les risques rattachés à des défauts de conception, et d’autre part, les risques associés à l’apprentissage machine. Pour avoir des principes et règles éthiques et dignes de confiance, l’IA doit respecter les valeurs de traçabilité, de transparence, d’explicabilité et de contrôle. Il s’agit de déployer et de gérer des systèmes de contrôle intelligents explicables, vérifiables, réutilisables et fiables.
L’usage omniprésent et invisible de l’intelligence Artificielle en entreprise soulève de nombreuses préoccupations en matière de sécurité et d’éthique :
- sécurité de fonctionnement autonome des machines,
- déshumanisation de prises de décision,
- dérive du monitoring par surveillance algorithmique des tâches
- exploitation des données personnelles,
- etc.
Les enjeux considérables de fiabilité des systèmes de l’IA concernent des dysfonctionnements potentiels majeurs dans l’entreprise de toute la chaine de production, d’administration ou de décision : pertes de données et de confiance, informations incohérentes, conduite erratique et dangereuse, etc. -
Les objets connectés portables engendrent aussi des risques professionnels nouveaux plus difficiles à appréhender dont la gestion est complexe et encore incertaine, car certains sont liés aux facteurs humains et à l’analyse comportementale.
La fuite de données personnelles et leur exploitation abusive suscite des craintes, mais le développement des objets connectés soulève aussi de nombreuses questions relatives aux facteurs psychologiques d’acceptabilité : crainte d’intrusion dans la vie personnelle et d’atteinte à la vie privée, inquiétude sur la surveillance constante et minutieuse de la présence, des efforts et de la rapidité de travail à seule fin d’accroitre la productivité. L’utilisation possible d’objets connectés implantés dans le corps sous la peau (puce RFID, NFC) accroîtra encore les problèmes éthiques dans le monde du travail, avec le sentiment de dépossession partielle de soi et d’espionnage permanent.
Sur la préservation de la vie privée du travailleur et la protection de ses données, si le RGPD apporte des éléments de réponses, il faut des dispositions nouvelles pour les travailleurs en matière d’accès aux données et à leur utilisation. Des règles en matière de surveillance, de suivi et de contrôle sont aussi nécessaires pour se protéger des risques d’exagération et de violation de leurs droits.
Une cybersécurité renforcée doit s'assurer que toutes les données sont cryptées. Les entreprises doivent être particulièrement vigilantes au traitement des données associées à l’identité du travailleur, aux personnes ayant accès à ces données et au stockage de ces données car ces données peuvent aussi être utilisées à des fins de surveillance. Ces dispositifs doivent se conformer à la fois aux règles dictées par la loi Informatique et Libertés (loi n° 78-17 du 6 janvier 1978) et au règlement européen sur la protection des données (RGPD de mai 2018) : principe de finalité, consentement et information des personnes et conservation limitée des données, droit à la portabilité des données, droit à l’oubli, droit à la limitation du traitement, droit d’opposition au profilage, désignation d’un Délégué à la Protection des Données. Une déclaration auprès de la CNIL est à déposer pour pouvoir traiter ces informations en toute légitimité. -
La multiplication des robots industriels et leur adaptation très rapide à un grand nombre de tâches manufacturières ou logistiques exposent les travailleurs à des risques pour leur sécurité : ceci est d’autant plus accentué dans les cas des nouveaux robots collaboratifs qui partagent un même espace de travail, en réalisant des travaux avec les opérateurs. Les dangers peuvent survenir lors de l’utilisation du robot mais aussi lors de sa maintenance ou de son réglage : risques mécaniques élevés de collision avec l’utilisateur, du fait notamment de la vitesse élevée d’exécution, du manque ou de la difficulté d’anticipation de certains mouvements des parties mobiles, de la force des impacts ... , risques psychologiques liés à l’interaction homme-machine (sentiments de dépendance, de perte d’autonomie et d’identité, excès de charge mentale ...).
La sécurité de l’homme dans les solutions robotisées passe par des dispositifs de protection et de signalisation matérielle et des barrières physiques pour les robots industriels « classiques », mais la sécurité des opérateurs pose des problèmes nouveaux pour les robots collaboratifs pour lesquels doivent être mises en œuvre des solutions de sécurité " immatérielle ", dans un espace ni délimité ni protégé, avec des techniques logicielles de vision et/ou de détection de collision à base de capteurs de contact et d’effort : l’objectif est d’anticiper, d’éviter les collisions ou d’en réduire les effets. Un élément essentiel de ces robots collaboratifs est donc de surveiller, de manière ciblée et sûre, tous les mouvements du robot afin de le stopper ou le dévier immédiatement si la vitesse ou la force exercée sont trop élevées. Il s’agit d’avoir à la fois un robot multitâche et qui n’ait plus aucun protecteur fixe tout en étant sûr.
Pour intégrer correctement la sécurité des robots collaboratifs, il faut fixer les paramètres de fonctionnement et de contrôle sécuritaire et ergonomique : vitesse maximale de collaboration, limite de puissance de force, surveillance de la distance de sécurité avec l’opérateur avec garantie de détection et de temps de réaction, gestion des événements imprévus ... Ce qui nécessite des capteurs électroniques mesurant les distances, les efforts, ... et un automate programmable et un logiciel dédié prenant en compte ces éléments et transmettant ses instructions à des organes actionneurs et effecteurs électriques et mécaniques.
Des normes techniques relatives à la robotique industrielle encadrent la relation homme-machine.
Les risques psychologiques, notamment avec l'usage de robots collaboratifs, sont encore peu connus par manque de recul et d'études, et il existe des lacunes entre les progrès réalisés dans l'application de la robotique industrielle et son large et croissante diffusion dans toutes les industries et la connaissance de leur impact sur la santé psychique et l'augmentation du stress au travail :
- les réponses organisationnelles à toutes les exigences de productivité entrainées par la robotisation qui s'étendent au personnel amené à travailler avec les robots, se caractérisent par une grande augmentation des pressions de toute nature sur les délais, la quantité, la qualité de la production.
- L'intensification de la charge mentale due aux nouvelles technologies informatiques ou d'automatisation est facteur de risque psychologique.
- L'isolement au sein d'équipes clairsemées et de vastes usines quasi-vides de présence humaine, la réduction d'autonomie, la perte d'identité face à des robots sont des conséquences possibles de la robotisation : interaction constante entre le travailleur et le robot, peu de communication avec son entourage, perte d'initiative ou marge de manœuvre dans les opérations, les cadences et la précision, dépendance à la machine ressentie comme excessive.
- Anxiété liée à l'évitement et à l'appréhension des contacts répétés avec le robot. -
Les nouvelles solutions exo-squelettiques au travail, motorisées (combinaison robotique) ou non, vont se propager rapidement dans de nombreux secteurs, ceux de la logistique ou de la préparation de commandes, des chantiers du BTP, des usines manufacturières (automobile, ...), de l’agriculture et des soins infirmiers etc.
Dans ce contexte de mutation du monde du travail et du développement de ces technologies, il est nécessaire de prendre en compte leurs impacts nouveaux sur la santé et la sécurité en entreprise : le port de l’exosquelette génère en effet de nouvelles contraintes liées à la proximité entre l’homme et le dispositif et à l’acceptation de la dépendance ... L’exosquelette induit ainsi des risques tels que des risques mécaniques dus à une défaillance technique, des risques physiques dus à un usage excessif ou inadapté avec de modifications gestuelles importantes, des risques psychologiques dus aux sentiments de perte d’autonomie, de charge mentale supérieure, des risques organisationnels d’exigence de rendement exagérée en cas d’accélération des cadences. -
Les outils de réalité virtuelle (RV) et augmentée(RA) de simulation offrent aux travailleurs l’opportunité d’une mise en situation virtuelle de risques, avec recherche de solutions pour faire face aux menaces d’accidents : les techniques de modélisation des risques et de simulation permettent d’appréhender les problèmes de sécurité au travail et de les résoudre fictivement, de travailler en équipe et de communiquer efficacement pour apporter des réponses adéquates à toutes les situations critiques potentielles.
- La simulation de risques, au travers de situations ciblées, est un moyen efficace de formation professionnelle : les plateformes de simulation sont des instruments d'apprentissage progressif et interactif et de développement rapide des compétences de gestion de risques, avec une vaste palette de différents médias numérisés performants qui s’appuient sur des logiciels et éventuellement des matériels connectés pour tester et simuler la sécurité au travail, et analyser les comportements individuels et collectifs en situation de crise. La formation des professionnels aux situations dangereuses, stressantes ou rares en réalité virtuelle permet la mise en place de scénarios confrontant le travailleur à ces situations avant de les rencontrer sur le terrain, améliorant considérablement sa pratique et sa gestion du stress. De même pour l’apprentissage de gestes techniques, le pilotage ou la maintenance d’équipements en réalité augmentée.
- L'utilisation d'un environnement 3D modulable en temps réel permet d’améliorer l'ergonomie des postes et/ou situations de travail dès la conception : la présentation des plans des installations de machines ou de bâtiments en réalité virtuelle permet d’identifier les accès aux différents composants, d’optimiser l’ergonomie générale des machines et de limiter les troubles musculosquelettiques, ou de prévenir les accidents de circulation des engins : grâce des objets connectés (casque immersif, écrans et lunettes 3D, capteurs de mouvement sur le corps, manette, tablette numérique ...), le travailleur, sous forme d'avatar, évolue à son poste de travail virtuel de manière hyperréaliste.
- Le BIM, Building Information Modeling (Modélisation des Données du Bâtiment), est une méthode de RV et RA, basée sur une maquette numérique et collaborative qui permet de créer et de gérer toutes les données techniques d’un bâtiment pour les différents corps de métiers, depuis son projet jusqu’à sa construction puis son exploitation. L’utilisation du BIM assure une meilleure prévention des risques en termes d’anticipation, de communication et de pédagogie : mieux identifier les risques, mieux les traiter, mieux sensibiliser les travailleurs avec des supports didactiques interactifs performants et ainsi travailler en meilleure sécurité.
Le rôle du CSSCT dans les réorganisations du travail de l’industrie 4.0
Si la conduite du changement a été mal mise en œuvre et n’a pas abouti à une bonne perception et acceptation des transformations des postes ou des relations de travail, du contenu, de la durée ou des cadences du travail, la Commission Santé Sécurité et Conditions de Travail (CSSCT) du CSE peut exprimer son besoin d'informations plus claires sur les organisations, sur les conditions de travail qui attendent les salariés après la restructuration, sur les charges de travail, sur l'aménagement des locaux, les changements d’horaires, les mobilités fonctionnelles ou géographiques, la formation à de nouvelles technologies notamment informatiques... et les conséquences de ces changements sur la santé, les conditions de travail, la sécurité et les perturbations de la vie sociale des salariés. Depuis la loi de modernisation sociale de janvier 2002, les prérogatives du CSSCT s’étendent à tous les domaines concernant la sécurité et la protection de la santé physique et mentale des salariés : ce qui englobe aussi l’aspect organisationnel pour laquelle l’instance doit être consultée. La CSSCT a le droit d’avoir recours à une expertise externe en cas de projet important modifiant les conditions d’hygiène et de sécurité ou les conditions de travail, afin de lui permettre d’avancer des propositions de prévention. Dans le cadre de sa mission générale d’analyse des conditions de travail et des actions de prévention qu’il peut proposer, la CSSCT peut alors estimer nécessaire de se faire assister d’un expert en analyse sociotechnique, recours justifié par l’impact important du projet vis-à-vis des conditions de travail, et par le nombre de salariés concernés par cette modification par rapport à l’effectif de l’établissement.
Pour aller plus loin :
• OFFICIEL PREVENTION : FORMATION CONSEILS FICHES MÉTIER : LA PRÉVENTION DES RISQUES DE LA ROBOTISATION INDUSTRIELLE : https://www.officiel-prevention.com/dossier/formation/fiches-metier/la-prevention-des-risques-de-la-robotisation-industrielle
• OFFICIEL PREVENTION : FORMATION CONSEILS FORMATION CONTINUE À LA SÉCURITÉ : RÉALITÉ VIRTUELLE ET RÉALITÉ AUGMENTÉE EN SANTÉ ET SÉCURITÉ AU TRAVAIL : https://www.officiel-prevention.com/dossier/formation/formation-continue-a-la-securite/realite-virtuelle-et-realite-augmentee-en-sante-et-securite-au-travail
• OFFICIEL PREVENTION : ORGANISATION ERGONOMIE LOGICIELS & APPLICATIONS DE SÉCURITÉ : LA PRÉVENTION DES RISQUES PROFESSIONNELS DE L’INTELLIGENCE ARTIFICIELLE : https://www.officiel-prevention.com/dossier/protections-collectives-organisation-ergonomie/logiciels-applications-de-securite/la-prevention-des-risques-professionnels-de-lintelligence-artificielle
• OFFICIEL PREVENTION : SANTÉ HYGIÈNE SST APPAREILS DE MESURE : OBJETS CONNECTÉS PORTABLES ET SANTÉ ET SÉCURITÉ DU TRAVAIL : https://www.officiel-prevention.com/dossier/sante-hygiene-medecine-du-travail-sst/appareils-de-mesure/objets-connectes-portables-et-sante-et-securite-du-travail
• OFFICIEL PREVENTION : PROTECTIONS INDIVIDUELLE LE CORPS : LA PRÉVENTION DES RISQUES PROFESSIONNELS DES EXOSQUELETTES : https://www.officiel-prevention.com/dossier/protections-individuelles/le-corps/la-prevention-des-risques-professionnels-des-exosquelettes
• INRS : Industrie du futur. Ce qu’il faut retenir : Comment concilier prévention des risques professionnels et industrie du futur ? (2021 - 12 pages)
• INRS : Industrie du futur : quels enjeux en santé et sécurité au travail ? (2019 - 32 pages)
Janvier 2022
Partagez et diffusez ce dossier
Laissez un commentaire
Votre adresse de messagerie ne sera pas publiée.